图书介绍
高炉炼铁过程优化与智能控制系统PDF|Epub|txt|kindle电子书版本网盘下载
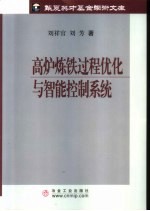
- 刘祥官,刘芳著 著
- 出版社: 北京:冶金工业出版社
- ISBN:7502432221
- 出版时间:2003
- 标注页数:270页
- 文件大小:54MB
- 文件页数:292页
- 主题词:高炉炼铁-过程-最佳化;高炉炼铁-智能控制-控制系统
PDF下载
下载说明
高炉炼铁过程优化与智能控制系统PDF格式电子书版下载
下载的文件为RAR压缩包。需要使用解压软件进行解压得到PDF格式图书。建议使用BT下载工具Free Download Manager进行下载,简称FDM(免费,没有广告,支持多平台)。本站资源全部打包为BT种子。所以需要使用专业的BT下载软件进行下载。如BitComet qBittorrent uTorrent等BT下载工具。迅雷目前由于本站不是热门资源。不推荐使用!后期资源热门了。安装了迅雷也可以迅雷进行下载!
(文件页数 要大于 标注页数,上中下等多册电子书除外)
注意:本站所有压缩包均有解压码: 点击下载压缩包解压工具
图书目录
上篇 开发篇3
1 高炉过程自动化概论3
1.1 跨世纪的技术难题——高炉炼铁过程自动化3
1.1.1 冶金科技发展的前沿课题3
1.1.2 自动化科学与技术的学科难题3
1.1.3 从基础自动化发展到信息网络化5
1.1.4 从“专家系统”迈向“智能控制自动化”5
1.1.5 从中国高炉炼铁实际出发,实现高炉炼铁过程智能自动化6
1.2 国内外高炉自动化进展的简要回顾7
1.2.1 高炉炼铁的基础自动化7
1.2.2 国外高炉自动化数学模型的研究进展8
1.2.3 国内高炉自动化研究中的计算机应用进展10
1.2.4 国内外高炉“专家系统”的简明对比13
1.3 高炉过程的系统优化与智能控制自动化14
1.3.1 应用“专家系统”是炼铁技术发展大趋势14
1.3.2 基础自动化与信息网络化是实现炼铁过程智能自动化的硬件基础15
1.3.3 智能控制自动化的两项重要模型基础16
2 高炉过程的工艺控制复杂性17
2.1 高炉冶炼进程中工长作业的复杂性与运筹控制17
2.1.1 炼铁工艺流程的主要组成工序17
2.1.2 值班工长的炉内作业、炉前作业与作业管理18
2.1.3 值班工长作业中的智力劳动19
2.1.4 值班工长对高炉进程的运筹控制19
2.2 高炉冶炼过程炉况故障状态的复杂性21
2.2.1 炉况的顺行状态21
2.2.2 异常炉况的主要种类22
2.2.3 异常炉况征兆与故障识别的数理逻辑诊断模型25
2.3 高炉过程控制的基础自动化与信息网络化27
2.3.1 槽下配料称量子系统的基础自动化28
2.3.2 卷扬上料布料子系统的基础自动化28
2.3.3 热风炉燃烧过程与富氧鼓风的基础自动化29
2.3.4 喷煤子系统的基础自动化29
2.3.5 炉前出铁出渣的机械化与信息采集30
2.3.6 化验室、过磅站终端计算机的联网与信息网络化30
2.4 高炉冶炼过程的控制复杂性31
2.4.1 控制复杂性的概念31
2.4.2 炉温控制与温度控制的本质区别31
2.4.3 炉温控制与炉况控制的交叉与运筹31
2.4.4 实时控制与预测控制组成的二步目标运筹控制32
2.4.5 调控优先级与调控3要素32
2.4.6 高炉冶炼过程复杂性的非线性机理探索33
3 高炉过程自动化的控制理论基础35
3.1 从传统控制理论到智能控制理论35
3.1.1 经典控制论的基本问题及其实现的控制35
3.1.2 现代控制论的基本问题和成就36
3.1.3 非线性控制系统的“能观性”与“能控性”39
3.2 智能控制理论的发展与应用39
3.2.1 智能控制论的由来39
3.2.2 智能控制论的“三元交集”40
3.2.3 智能控制论面临的复杂性40
3.2.4 高炉“专家系统”面对智能控制论41
3.3 从自动控制理论基础思考高炉炼铁自动化难题41
4 高炉过程数学模型的复杂性43
4.1 高炉冶炼过程的多目标系统优化模型43
4.1.1 高炉过程的物质流与信息流分析43
4.1.2 高炉过程参数的层次结构分析43
4.1.3 高炉过程信息流的数据融合44
4.1.4 高炉过程参数的滤波分析46
4.1.5 高炉冶炼过程多目标系统优化模型的建立47
4.2 高炉过程数学模型的复杂结构48
4.2.1 关于数学模型技术48
4.2.2 工艺计算的数量化模型48
4.2.3 概率统计模型49
4.2.4 模糊控制模型49
4.2.5 数理逻辑推断模型50
4.3 基于时间序列的变频统计与冶炼过程优化控制规律50
4.3.1 描述复杂工艺系统过程状态的时间序列图50
4.3.2 高炉冶炼过程的“混沌相似性”51
4.3.3 变频统计方法的数学原理52
4.3.4 基于四元时间序列图的样本空间模型52
4.3.5 高炉冶炼过程的优化控制规律52
4.4 基于平稳时间序列的炉温预测与控制55
4.4.1 炉温[Si]控制对高炉过程控制的意义55
4.4.2 考察炉温变动规律的软件仪表——炉温智能控制图56
4.4.3 炉温预报“命中率”与“成功率”的灵活应用57
4.5 炉温[Si]的智能控制偏微分方程58
4.5.1 炉温控制偏微分方程58
4.5.2 炉温控制方程的多元回归算法的局限性58
4.5.3 正交试验设计证明工艺经验的正确性与差异性59
4.5.4 Bellman动态规划与神经网络算法59
5 高炉过程的智能控制自动化61
5.1 高炉过程运筹与控制的两种策略61
5.1.1 第一类策略:以改善“硬条件”为基础的控制策略61
5.1.2 第二类策略:基础自动化+信息网络化+系统优化的控制策略62
5.2 高炉冶炼过程智能控制自动化系统的设计63
5.2.1 高炉过程的最佳状态与随机最优控制63
5.2.2 炉况等级判断的自动化64
5.2.3 炉况故障诊断与报警的自动化64
5.2.4 信息传送自动化与“专家系统”的三位一体应用67
5.2.5 高炉冶炼过程的智能控制自动化主流程67
5.3 智能控制自动化的计算机网络基础69
5.3.1 “智能控制专家系统”的计算机网络概述69
5.3.2 铁区的信息传送网络70
5.3.3 炼铁厂管理决策与技术分析的办公自动化网络71
5.4 智能控制自动化系统的软件设计72
5.4.1 三层结构的软件设计72
5.4.2 软件系统的主要功能模块73
6 “高炉炼铁优化专家系统”的应用工程与效益75
6.1 案例1:“炼铁优化专家系统”在济钢350m3高炉上的应用75
6.1.1 概述75
6.1.2 “炼铁优化专家系统”的设计76
6.1.3 “炼铁优化专家系统”的特色——软件仪表77
6.1.4 “炼铁优化专家系统”的应用成效与效益82
6.1.5 结语82
6.2 案例2:“新临钢380m3高炉优化专家系统”的应用实践83
6.2.1 概述83
6.2.2 “专家系统”的构成83
6.2.3 对冶强的优化85
6.2.4 炉温[Si]和渣碱度(R)的优化选择86
6.2.5 对鼓风动能的优化87
6.2.6 结语88
6.3 案例3:“莱钢1号750m3高炉智能控制专家系统”89
6.3.1 概述89
6.3.2 “智能控制专家系统”的信息网络化基础89
6.3.3 “智能控制专家系统”的功能设计91
6.3.4 “智能控制专家系统”的主要功能模块92
6.3.5 网络版“智能控制专家系统”的应用效益96
6.3.6 高炉冶炼过程智能控制自动化发展前景97
下篇 应用篇103
1 系统概述与数据录入103
1.1 引言103
1.2 系统概述104
1.2.1 【系统】钮的功能子菜单104
1.2.2 【管理】钮功能展开105
1.2.3 【视图】108
1.2.4 【登录】109
1.2.5 【数据库】109
1.2.6 【优化】109
1.2.7 【炉况】110
1.2.8 【报表】110
1.2.9 【导航】钮110
1.3 数据录入的规则与注意事项110
1.3.1 确认录入数据的有效位置110
1.3.2 清除旧数据或部分修改旧数据111
1.3.3 用鼠标或键盘移动光标时的特点111
1.3.4 用【Tab】键从一个栏目向男一栏目快速移动光标111
1.3.5 使用快捷数字键,提高数据录入效率112
1.3.6 输入汉字信息的操作112
1.4 数据表的通用功能钮112
1.4.1 【添加】钮112
1.4.2 【修改】钮113
1.4.3 【查询】钮113
1.4.4 【删除】钮113
1.4.5 【最前】钮114
1.4.6 【最后】钮114
1.4.7 【上一条】114
1.4.8 【下一条】114
1.5 录入数据的工艺顺序与注意事项114
1.5.1 数据表输入数据的先后顺序114
1.5.2 输入、修改数据的前提条件115
1.5.3 关于录入数据【可能出错】的智能化判断115
2 数据库与数据表116
2.1 原燃料数据116
2.1.1 原料表116
2.1.2 焦炭表118
2.1.3 煤粉表118
2.1.4 炮泥数据表118
2.1.5 单价表118
2.2 常规作业数据119
2.2.1 作业表119
2.2.2 出铁表121
2.2.3 炉渣分析表122
2.2.4 出渣表123
2.2.5 煤气表124
2.3 作业变更数据125
2.3.1 上料布料表(变料表)125
2.3.2 调剂指令表126
2.3.3 故障记录表126
2.3.4 炉料采集计算表126
2.4 专家知识库128
2.4.1 专家知识规则表128
2.4.2 调控系数表129
2.4.3 输入检查提示129
2.4.4 人工智能库130
2.5 风口渣口数据131
2.5.1 喷煤风口表131
2.5.2 风口更换表132
2.5.3 风口状态表133
2.6 温度压力数据134
2.6.1 本体温度数据134
2.6.2 炉底温度数据137
2.6.3 压力数据表138
2.7 冷却系统数据138
2.7.1 汽化冷却系统138
2.7.2 风渣口冷却数据138
2.8 事务记录139
2.8.1 值班记录139
2.8.2 高炉大事记139
2.8.3 车间文件140
2.8.4 气象数据140
2.9 班组考核140
2.9.1 日炉前指标考核140
2.9.2 月炉前指标考核141
2.9.3 班组统计141
2.9.4 班组综合信息141
2.10 成本核算142
2.10.1 日成本142
2.10.2 月成本142
2.11 生产统计143
2.11.1 日统计143
2.11.2 月统计144
2.11.3 年统计144
2.12 基本参数144
2.12.1 高炉设计参数144
2.12.2 用户登记表146
3 过程优化与智能控制147
3.1 炉温预报148
3.1.1 炉温发展趋势148
3.1.2 [Si]-[S]数值预报检验150
3.1.3 炉温的四元时间序列综合判断152
3.1.4 炉温的预测控制153
3.2 配料布料155
3.2.1 简要原理说明155
3.2.2 炉料校核单的计算156
3.2.3 煤气曲线优化159
3.3 图表监测159
3.3.1 24小时喷煤速率与喷煤量监测图160
3.3.2 炉体温度场轴向图160
3.3.3 炉体温度场径向图161
3.3.4 炉底侵蚀状态图162
3.3.5 炉喉十字测温图163
3.4 优化决策166
3.4.1 优化决策模型原理166
3.4.2 系统样本划分167
3.4.3 系统优化分析表的调阅与打印169
3.4.4 系统优化分析图总结生产优化规律170
3.4.5 产量质量优化分析图174
3.5 冶炼强度的优化182
3.5.1 变频统计优选183
3.5.2 等步长统计优选185
3.6 时间序列分析187
3.6.1 时间序列分析原理187
3.6.2 时间序列图的功能与操作188
3.6.3 原燃料条件时间序列190
3.6.4 上料制度时间序列191
3.6.5 送风制度时间序列192
3.6.6 出渣出铁时间序列192
3.6.7 炉体温度场时间序列194
3.7 统计分布分析196
3.7.1 原燃料条件对比197
3.7.2 上料制度对比198
3.7.3 送风制度对比199
3.7.4 出渣出铁对比200
3.7.5 炉体温度场对比200
4 高炉冶炼行程的炉况诊断203
4.1 炉况诊断的工作原理203
4.1.1 简要说明203
4.1.2 炉况诊断模块的操作使用步骤204
4.2 炉况等级综合判断星形图204
4.2.1 炉况等级综合判断图工作原理204
4.2.2 炉况等级星形图的操作与使用205
4.3 炉况顺行状态诊断206
4.3.1 关于炉况顺行状态诊断的若干说明206
4.3.2 炉况顺行状态诊断的操作与判断206
4.4 炉墙结厚、结瘤与顽固性结瘤诊断207
4.4.1 炉墙结厚、结瘤与顽固性结瘤逻辑诊断图的原理207
4.4.2 炉瘤故障逻辑诊断图的操作与使用208
5 高炉作业管理报表210
5.1 高炉作业管理的办公自动化210
5.2 管理报表模块的使用通则210
5.2.1 选择、预览管理报表211
5.2.2 退出报表预览及打印报表211
5.2.3 统计台账的汇总方式与灵活应用212
5.3 整理记录1的操作使用212
5.3.1 生铁产量完成情况表212
5.3.2 主要冶炼指标和生铁成分表213
5.3.3 炉渣分析及渣量表213
5.3.4 送风制度调剂情况表218
5.4 整理记录2的操作使用219
5.4.1 入炉原燃料成分表219
5.4.2 高炉原燃料消耗情况表220
5.4.3 高炉煤气分析表220
5.5 月统计台账的操作使用226
5.5.1 月台账1的操作使用226
5.5.2 月台账2的操作使用228
5.5.3 月台账3的操作使用228
5.6 高炉操作日志230
5.6.1 关于“高炉操作日志”的说明230
5.6.2 高炉送风作业日报表(高炉送风作业及本体温度日报)231
5.6.3 出铁情况日报表231
5.6.4 矿石分析日报表231
5.6.5 炉料配比日报表231
5.6.6 风口工作状态日报表236
6 炉温的智能控制238
6.1 炉温智能控制原理238
6.1.1 炉温调控的工艺操作经验基础238
6.1.2 现代控制论与智能控制论原理239
6.1.3 炉温控制预测的偏微分方程与神经网络算法240
6.2 炉温智能控制图241
6.2.1 主要功能钮的使用242
6.2.2 [Si]-[S]控制预测图的使用244
6.2.3 状态变量直方图的使用244
6.2.4 控制变量直方图的使用245
6.2.5 每30min1次的炉温智能控制提示245
6.2.6 人机交互的炉温智能控制指示图245
6.3 炉温智能控制系统图的综合应用246
6.3.1 [Si]-[S]预测控制图的仿真应用246
6.3.2 炉温发展过程预测的人机交互验证与自学习247
6.3.3 提高炉温控制的命中率和成功率247
7 化验数据输入子系统的使用248
7.1 系统概述248
7.1.1 引言248
7.1.2 启动系统248
7.2 数据输入250
7.2.1 功能钮的操作使用250
7.2.2 化验数据表的数据录入251
7.3 异常情况的处理256
7.3.1 死机问题的处理256
7.3.2 “子系统”瘫痪的处理256
7.3.3 无法登录“子系统”的处理257
8 冶炼参数系统优化分析报告与生产优化建议258
8.1 引言258
8.2 生产数据的基本统计258
8.3 应用“智能控制专家系统”进行系统分析259
8.3.1 系统分析表对3个月生产的总结对比259
8.3.2 利用系统优化分析图观察、总结高炉的生产优化规律261
8.3.3 冶炼强度的系统优化262
8.4 原燃料条件变化下的对策优化263
8.4.1 烧结矿质量波动的时间序列图263
8.4.2 两个时间段的烧结矿质量变动统计对比图263
8.4.3 烧结矿质量变动的统计对比与差异显著性检验264
8.5 关于用好“智能控制专家系统”的建议264
8.5.1 关于技术分析与管理决策上的应用264
8.5.2 关于工长应用“专家系统”的技术培训265
8.5.3 关于与“专家系统”应用配套的工艺措施265
参考文献266