图书介绍
特种加工成形手册 上PDF|Epub|txt|kindle电子书版本网盘下载
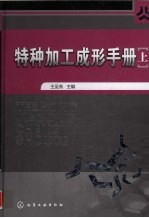
- 王至尧主编 著
- 出版社: 北京:化学工业出版社
- ISBN:7122053169
- 出版时间:2009
- 标注页数:569页
- 文件大小:358MB
- 文件页数:580页
- 主题词:
PDF下载
下载说明
特种加工成形手册 上PDF格式电子书版下载
下载的文件为RAR压缩包。需要使用解压软件进行解压得到PDF格式图书。建议使用BT下载工具Free Download Manager进行下载,简称FDM(免费,没有广告,支持多平台)。本站资源全部打包为BT种子。所以需要使用专业的BT下载软件进行下载。如BitComet qBittorrent uTorrent等BT下载工具。迅雷目前由于本站不是热门资源。不推荐使用!后期资源热门了。安装了迅雷也可以迅雷进行下载!
(文件页数 要大于 标注页数,上中下等多册电子书除外)
注意:本站所有压缩包均有解压码: 点击下载压缩包解压工具
图书目录
第1篇 概论1
第1章 材料特种加工及其在现代制造业中的作用3
1 特种加工的定义和特点3
1.1 特种加工的定义3
1.2 特种加工的特点3
2 特种加工的产生和发展4
2.1 特种加工的产生4
2.2 增材加工——特种加工的新进展4
3 特种加工的分类及工艺性能比较5
3.1 特种加工的分类5
3.2 特种加工工艺性能比较7
第2章 材料特种加工成形工程的特点与要求8
1 特种加工对结构工艺性等的影响8
2 现代制造业的发展对特种加工的新要求8
2.1 模具加工指标的微细化对特种加工的新要求8
2.2 微电子机械系统对特种加工的新要求9
2.3 航空航天工业对特种加工的新要求10
2.4 纳米技术对特种加工的新要求10
第3章 材料成形特种加工技术在工程中的应用11
1 特种加工在现代制造业中的作用11
1.1 特种加工在现代模具制造工业中的作用11
1.2 特种加工技术在航天发动机制造中的应用11
2 快速原型与制造技术在材料成形工程中的应用12
2.1 新产品开发过程中的设计验证与功能验证12
2.2 基于快速原型的快速制造工艺12
3 RP技术在航天工业中的应用16
4 橡皮垫板成形技术及其在工程中的应用17
4.1 橡皮垫板成形技术的起源与发展17
4.2 橡皮垫板成形装备技术和应用17
5 热等静压/粉末冶金(HIP/PM)技术18
5.1 热等静压/粉末冶金技术的起源和发展18
5.2 热等静压/粉末冶金技术的应用18
第4章 材料特种加工成形工程的技术发展动态和趋势19
1 特种加工技术的发展动态19
1.1 总的发展态势19
1.2 特种加工技术发展状况19
2 材料特种加工成形工程展望23
2.1 特种加工技术向微细化方向发展23
2.2 特种加工技术向高精度方向发展23
2.3 特种加工技术向信息化方向发展24
2.4 特种加工技术向智能化方向发展25
2.5 特种加工技术向集成化方向发展27
参考文献28
第2篇 材料电火花成形加工技术29
第1章 概述31
1 电火花加工的特点31
2 电火花加工的工艺类型及适用范围31
3 电火花加工对材料可加工性和结构工艺性等的影响32
第2章 电火花加工的基本原理和机理33
1 电火花加工常用术语和符号33
2 电火花加工的基本原理35
3 电火花加工的机理36
第3章 电火花加工中的基本规律39
1 影响放电蚀除量的主要因素39
1.1 极性效应的影响39
1.2 电参数对电蚀量的影响39
1.3 金属材料热学物理常数对电蚀量的影响40
1.4 工作液对电蚀量的影响40
1.5 影响电蚀量的一些其他因素41
2 电火花加工的加工速度和工具电极的损耗速度41
2.1 加工速度41
2.2 工具电极相对损耗速度和相对损耗比41
3 影响电火花加工精度的主要因素42
4 电火花加工的表面质量43
4.1 表面粗糙度43
4.2 表面变质层43
4.3 表面机械性能44
第4章 电火花加工工艺参数及其曲线图表46
1 电火花加工的工艺参数46
2 材料、脉宽、峰值电流与表面粗糙度的关系54
3 材料、脉宽、峰值电流与单边放电间隙的关系54
4 材料、脉宽、峰值电流与蚀除速度的关系54
5 材料、脉宽、峰值电流与电极损耗率的关系55
6 正确选择电火花加工工艺参数规准的方法55
第5章 电火花成形加工机床56
1 电火花成形加工机床主机及附件56
1.1 电火花成形加工机床主机57
1.2 电火花成形加工机床用附件71
2 电火花加工用的工作液过滤系统76
2.1 工作液过滤系统的主要组成部分和作用77
2.2 工作液过滤系统设计和使用时的注意事项77
2.3 对过滤器结构的要求和选择78
2.4 工作液的作用和选择79
3 电火花加工用的脉冲电源81
3.1 概述81
3.2 脉冲电源的脉冲波形及分类82
3.3 RC线路脉冲电源83
3.4 可控硅(又称晶闸管)式脉冲电源83
3.5 晶体管式脉冲电源84
3.6 精密数控电火花成形机床的脉冲电源86
3.7 智能化脉冲电源及脉冲电源的发展趋势87
4 电火花加工用的伺服进给系统88
4.1 概述88
4.2 伺服进给系统的放电间隙检测环节90
4.3 步进电动机伺服进给系统91
4.4 直流伺服电动机自动伺服进给调节系统92
4.5 交流伺服电动机伺服进给调节系统93
4.6 直线电动机自动进给调节系统94
第6章 电火花穿孔加工工艺96
1 电火花简单穿孔、套料加工96
1.1 打去断入工件中的钻头、丝锥96
1.2 电火花套料加工96
1.3 电火花加工拉丝模97
1.4 电火花加工特殊型孔零件98
2 冲模电火花加工的要点99
2.1 冲模电火花加工的基本工艺方法99
2.2 简单方孔冲模的电火花加工102
2.3 电机转子冲孔落料模加工103
2.4 钟表齿轮精密冷模加工103
3 小孔、小深孔、异形小孔、多孔、微孔等电火花加工104
3.1 小孔电火花加工104
3.2 小深孔的电火花加工105
3.3 异形小孔的电火花加工107
3.4 多孔的电火花加工108
3.5 微孔电火花加工109
4 超声波电火花复合加工小孔109
4.1 复合加工装置组成及原理109
4.2 超声电火花复合加工的主要规律110
第7章 电火花成形加工工艺112
1 电火花成形加工工艺方法112
1.1 单工具电极直接成形法112
1.2 单工具电极平动(摇动)加工法113
1.3 手动侧壁修光法114
1.4 分解工具电极法114
1.5 多工具电极更换法115
2 单轴数控电火花成形加工工艺及加工实例115
2.1 对开模(无毛边模具)加工实例115
2.2 洗衣机调节螺母注塑模加工实例116
2.3 锥齿轮精锻模加工实例116
2.4 塑料叶轮注塑模加工实例117
2.5 高精度压胶型腔模加工实例118
2.6 用平动(摇动)功能加工内螺纹120
3 多轴数控电火花成形加工工艺及加工实例120
3.1 NCEDM(数控电火花加工)的多坐标系设定技术121
3.2 NCEDM先进的自动定位技术和在机检测技术121
3.3 NCEDM的多功能、多方式的摇动技术125
3.4 NCEDM编程使用的基本指令介绍129
3.5 NCEDM的多种加工方式129
3.6 加工规准的选择、转换,摇动(平动)量的分配和电极尺寸的设计132
3.7 多轴数控电火花成形加工实例137
3.8 数控电火花成形加工机床的编程和选择规准举例141
4 电火花铣削加工技术143
4.1 电火花铣削加工技术的产生及特点143
4.2 电火花铣削加工中的电极损耗补偿技术144
4.3 基于分层制造的电极等损耗电火花铣削加工技术145
5 微细电火花加工技术148
5.1 微细电火花加工的特点与实现条件148
5.2 微细电极的在线制作149
5.3 电火花加工装置的微型化150
5.4 微细电火花加工的应用举例151
第8章 其他电火花加工技术153
1 混粉大面积镜面光整电火花加工153
1.1 大面积电火花镜面加工的探索和难点153
1.2 混粉电火花镜面加工的原理和机理153
1.3 混粉大面积电火花镜面加工试验研究154
1.4 新型混粉电火花镜面加工装置的研制154
1.5 混粉大面积电火花镜面光整加工实例155
2 电火花磨削加工156
2.1 薄壁低刚度工件(蜂窝结构)的电火花磨削157
2.2 成形表面的电火花磨削158
2.3 窄槽类零件电火花加工工艺159
2.4 薄肋类零件电火花加工工艺160
2.5 深小通孔的电火花磨削161
2.6 轧辊电火花毛化162
2.7 低刚度细长锥杆电火花磨削162
3 双轴共轭回转式和展成回转式电火花加工新技术163
3.1 双轴共轭回转式电火花加工163
3.2 展成回转式电火花加工168
3.3 回转式电火花加工的技术特点和适用面171
3.4 实现精密级电火花加工的技术条件172
3.5 回转式电火花加工典型工艺实例分析173
3.6 回转式电火花加工典型机床178
4 特殊材料和非导电材料的电火花加工179
4.1 聚晶金刚石等超硬材料的电火花加工180
4.2 非导电材料的电火花加工181
5 电火花表面强化改性及沉积技术184
5.1 气体中电火花表面强化(改性)184
5.2 气体中电火花刻字工艺及装置185
5.3 气体中放电沉积堆积造型185
5.4 钛合金水中电火花放电着色185
5.5 油中电火花放电沉积表面改性处理186
6 气体介质中电火花加工188
6.1 气体介质中电火花加工原理189
6.2 气体介质中电火花三维形状加工189
6.3 气体介质中电火花加工特性189
6.4 气体介质中电火花加工特点191
7 微弧氧化表面处理技术191
7.1 微弧氧化后的表面陶瓷层的功能和作用191
7.2 微弧氧化表面处理技术的工艺特点191
7.3 微弧氧化工艺及设备的原理191
7.4 微弧氧化过程的机理——电极间的反应192
7.5 微弧氧化技术在铝、镁、钛等合金中的应用前景192
第9章 电火花加工中的防火、技术保安及无害化193
1 我国对电火花加工机床的安全和对环境影响的国家强制标准193
2 电火花加工中的技术保安及防火194
2.1 电火花加工中的技术安全规程194
2.2 正确执行电火花加工安全操作规程194
2.3 做到岗位责任制和文明生产的各项要求195
3 电火花加工的无害化及绿色制造196
参考文献197
第3篇 材料数控电火花线切割技术199
第1章 概论201
1 电火花加工的分类201
2 电火花线切割加工原理201
2.1 电火花线切割加工基本原理201
2.2 电火花线切割加工物理过程202
2.3 电极丝动态特性203
3 电火花线切割加工的特点及分类207
3.1 电火花线切割加工特点207
3.2 电火花线切割加工的应用范围207
3.3 电火花线切割机分类208
4 电火花线切割技术的研究现状及发展趋势210
4.1 电火花线切割技术的研究现状210
4.2 我国电火花线切割技术的近期进步212
4.3 我国电火花线切割技术的发展趋势及主要任务213
第2章 数控电火花线切割设备215
1 概述215
1.1 基本组成215
1.2 型号规格及参数标准215
1.3 机床精度标准及检验方法216
1.4 使用规则及维护保养222
2 机床本体223
2.1 机床结构223
2.2 运丝系统227
2.3 锥度切割装置232
2.4 电火花线切割机的自动穿丝系统233
2.5 进电方式233
2.6 工作液及其循环系统234
3 脉冲电源236
3.1 基本要求及组成236
3.2 高速走丝脉冲电源电路分析240
3.3 低速走丝脉冲电源242
3.4 适应控制电源243
4 数控装置与机床电气244
4.1 数控功能要求、结构与分类244
4.2 伺服进给245
4.3 机床电气246
第3章 电火花线切割机控制系统及编程248
1 插补原理248
1.1 逐点比较法插补原理248
1.2 双判别进给插补原理251
2 锥度加工原理254
2.1 控制基本原理254
2.2 顺倒锥度加工255
2.3 锥度加工插补方法257
3 上下异形加工原理262
3.1 直纹面构造的几何机理262
3.2 工件上下面轨迹线性化处理263
3.3 上下线架投影轨迹计算265
3.4 一种上下异形比例插补方法266
3.5 四轴联动编程简要算法框图及计算实例267
3.6 上下线架图形轨迹联动简介269
4 程序格式及编程方法272
4.1 程序格式272
4.2 基本编程方法276
5 单板与单片机控制器部分电路分析281
6 基于PC机大线切割控制与接口技术285
6.1 PC机编程与控制285
6.2 串行通信288
6.3 PC机接口技术290
7 自动编程294
7.1 语言式微机编程294
7.2 绘图式自动编程系统296
7.3 切割编程298
7.4 自动编程系统的其他功能304
第4章 电火花线切割加工的基本规律307
1 电火花线切割加工的工艺指标及测试方法307
1.1 主要工艺指标307
1.2 常用的测试方法307
1.3 各工艺指标之间的关系309
2 影响切割速度的主要因素310
2.1 脉冲参数对切割速度的影响311
2.2 非电参数对切割速度的影响312
3 影响加工精度的主要因素316
3.1 加工尺寸精度316
3.2 形位精度318
4 影响加工表面质量的主要因素319
4.1 影响加工表面粗糙度主要因素319
4.2 影响切割条纹的主要因素320
4.3 影响加工表面组织变化层的主要因素320
5 影响电极丝损耗的主要因素321
5.1 脉冲参数321
5.2 脉冲波形322
5.3 电极丝材料及移动速度322
5.4 工作液323
第5章 数控电火花线切割加工工艺及应用324
1 基本工艺路线及工艺分析324
1.1 线切割加工基本工艺路线及应用场合324
1.2 零件图纸工艺分析324
1.3 影响正常加工的主要因素325
1.4 工序安排326
1.5 编程的工艺性327
2 电火花线切割加工前的工艺准备330
2.1 工件备料330
2.2 工件装夹332
2.3 数控电火花线切割机床的调整336
2.4 加工参数设置与调整340
3 电火花线切割加工多次切割工艺343
3.1 电火花线切割加工的工艺类型343
3.2 多次切割的必要性及其应具备的条件345
3.3 电极丝的空间形位变化345
3.4 多次切割工艺及其效果347
4 大厚度工件电火花线切割348
4.1 切缝中工作液的流动状态348
4.2 实现大厚度工件稳定切割的途径349
4.3 大厚度工件线切割工艺350
4.4 大厚度工件切割实例351
5 电火花线切割加工工艺应用实例351
5.1 冲裁模加工351
5.2 一次同时加工出凸模与凹模352
5.3 超行程工件的加工353
5.4 锥度零件的加工354
5.5 零件加工实例356
第6章 现代制造技术在电火花线切割中的应用358
1 现代制造技术358
1.1 概述358
1.2 WEDM中的现代制造技术研究内容359
2 电火花线切割的计算机仿真364
2.1 电火花线切割加工计算机仿真技术概述364
2.2 电火花线切割加工神经网络模型366
2.3 高速走丝电火花线切割加工工艺效果仿真系统368
2.4 大厚度切割仿真系统370
2.5 其他仿真方法在电火花线切割中的应用372
3 电火花线切割加工CAD/CAM系统372
3.1 概述372
3.2 电火花线切割加工的CAD/CAM系统373
4 电火花线切割智能加工系统377
4.1 智能制造技术概述377
4.2 电火花线切割智能加工系统377
4.3 电火花线切割智能加工系统主要模块380
参考文献388
第4篇 材料电化学加工技术389
第1章 电解加工基本原理391
1 电解加工过程的电化学基础391
1.1 电解和电解加工391
1.2 电极电位、电极反应及电极反应的顺序392
1.3 外电场作用下电极的极化及实际电解加工过程的电极反应394
1.4 电解去除量的计算——法拉第定律和电流效率397
1.5 加工间隙的形成及其对电解加工成形的决定作用399
2 电解加工间隙中的电场特性399
2.1 电场的物理描述399
2.2 电解加工间隙中的电场分布400
2.3 基于电场分布的电解加工成形规律研究401
3 电解加工间隙中的流场402
3.1 电解加工间隙中的流动特性——气液两相流动402
3.2 基于流场分析的电解加工成形规律404
4 电解加工间隙及电解加工成形规律的综合分析405
4.1 加工过程的基本微分方程及应用405
4.2 理想电解加工过程和成形规律408
4.3 非理想电解加工过程及其成形规律408
第2章 电解加工工艺基础411
1 电解加工工艺及工艺参数411
1.1 电解加工工艺特点411
1.2 电解加工工艺参数及其对加工的影响413
1.3 工艺参数的选择414
2 电解液415
2.1 电解液的作用、要求及分类415
2.2 电解液选择原则及常用电解液415
2.3 混气电解加工及混气电解液419
3 电解加工的流场设计420
3.1 电解液流动形式420
3.2 电解液流速和进口压力422
3.3 流场均匀性设计424
3.4 混气电解加工气液混合器及其设计426
3.5 电解加工流场设计实例428
4 电解加工精度432
4.1 电解加工精度及加工误差432
4.2 影响电解加工精度的基本规律432
4.3 提高加工精度的工艺途径438
5 电解加工表面质量439
5.1 电解加工表面质量的特点439
5.2 电解加工表面粗糙度及其影响因素439
5.3 电解加工可能产生的表面缺陷及相应防止措施439
5.4 电解加工表面质量对零件疲劳强度的影响440
第3章 电解加工设备442
1 电解加工设备的总体论述442
1.1 电解加工设备的组成和功能442
1.2 电解加工设备的分类和选型442
1.3 电解加工设备的总体设计原则442
2 电解加工机床444
2.1 机床的构成及特点444
2.2 电解加工机床总体方案的制定445
2.3 机床主要部件的典型方案447
2.4 两类常用电解加工机床简介452
3 电解液系统457
3.1 电解液系统的功能及其特点457
3.2 两种典型的电解液系统457
3.3 电解液系统各部件的选用原则457
4 电解加工电源及短路保护系统461
4.1 电解加工电源的基本要求461
4.2 电解加工电源的基本类型461
4.3 快速短路保护的特点467
4.4 两种有代表性的直流电源短路保护系统468
5 电解加工自动控制系统470
5.1 控制系统的组成、功能及控制模式470
5.2 电解加工设备控制系统的典型方案及典型元件471
6 电解加工工艺装备474
6.1 工艺装备的功能及特殊要求474
6.2 特殊材料的选用及结构设计中的特殊问题474
6.3 几种夹具结构的实例475
第4章 电解加工的应用477
1 概述477
1.1 电解加工应用概况477
1.2 选用电解加工工艺的基本原则477
2 模具型面加工477
2.1 模具型面电解加工特点及应用范围477
2.2 模具型面电解加工工艺477
2.3 典型应用实例480
3 叶片型面加工482
3.1 叶片电解加工的应用特点、分类和范围482
3.2 叶片电解加工工艺484
3.3 电解加工叶片的典型实例486
4 深小孔、型孔电解加工488
4.1 深小孔电解加工488
4.2 型孔电解加工491
5 枪、炮管膛线电解加工493
5.1 膛线电解加工的特点和分类493
5.2 膛线电解加工工艺494
5.3 膛线电解加工新技术的应用实例496
6 整体叶轮加工498
6.1 等截面叶片整体叶轮电解套型加工498
6.2 变截面扭曲叶片整体叶轮加工498
6.3 应用实例500
7 电化学去毛刺500
7.1 概述500
7.2 电化学去毛刺的工艺特点501
7.3 电化学去毛刺的设备502
7.4 电化学去毛刺应用实例502
7.5 电化学去毛刺的新发展503
第5章 电解加工新技术505
1 脉冲电流电解加工505
1.1 脉冲电流电解加工的基本特征505
1.2 低频、宽频冲电流电解加工507
1.3 高频、窄脉冲电流电解加工508
2 数控展成电解加工515
2.1 数控展成电解加工系统组成516
2.2 旋转阴极展成电解加工516
2.3 “单直线刃”喷射式阴极展成电解加工518
2.4 整体叶轮的数控展成电解加工520
3 小间隙电解加工523
3.1 小间隙电解加工的工艺特点523
3.2 设备保障条件527
3.3 典型应用527
4 小孔电液束加工528
4.1 电液束加工工艺要点528
4.2 电液束加工的应用529
5 电解擦削530
5.1 电解擦削装置简介530
5.2 电解擦削工艺要点532
5.3 应用实例533
6 微细电解加工535
6.1 微细电解加工的基础条件535
6.2 微细电解加工方法536
6.3 复合微细电解加工研究方向537
第6章 电铸成形和电刷镀加工538
1 电铸成形加工原理538
1.1 加工原理538
1.2 电铸金属沉积质量的计算和电铸成形速度538
1.3 电场、流场设计539
2 电铸工艺541
2.1 电铸工艺条件和工艺参数及其对电铸速度、质量的影响541
2.2 提高电铸速度、改进电铸质量的措施541
3 电铸的应用和发展543
3.1 电铸的典型应用543
3.2 电铸技术的发展趋势546
4 电刷镀加工547
4.1 加工原理547
4.2 工艺要点547
4.3 电刷镀的典型应用548
第7章 复合电化学加工550
1 电解磨削550
1.1 电解磨削加工原理550
1.2 电解磨削工艺和设备550
1.3 电解磨削典型应用552
2 电解磨料光整加工553
2.1 电解磨料光整加工机理与特点553
2.2 工艺参数对光整加工质量的影响及参数选择554
2.3 典型应用与发展556
3 超声-电解复合加工557
3.1 超声-电解复合加工原理及工艺特点557
3.2 研究现状和应用前景560
4 电解-电火花复合加工560
4.1 电解-电火花复合加工原理及工艺特点560
4.2 电解-电火花复合加工的研究、应用和发展561
第8章 电化学加工技术的发展趋势565
1 基于电化学加工原理和复合加工原理而不断创新、发展新加工技术565
1.1 高频、窄脉冲电流电解加工565
1.2 高速、高压、小间隙电解加工565
1.3 数控电解加工565
1.4 复合电化学加工565
2 计算机控制技术将得到更高水平的应用566
2.1 电化学加工过程(参数)的自动控制566
2.2 CAD/CAM技术、数字化制造技术的应用566
2.3 提高加工设备的计算机控制水平566
3 微细电化学加工技术探索566
4 绿色电化学加工567
参考文献568