图书介绍
高速硬态切削加工及其稳定性研究PDF|Epub|txt|kindle电子书版本网盘下载
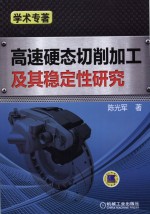
- 陈光军著 著
- 出版社: 北京:机械工业出版社
- ISBN:9787111469735
- 出版时间:2014
- 标注页数:158页
- 文件大小:25MB
- 文件页数:167页
- 主题词:高速切削-研究
PDF下载
下载说明
高速硬态切削加工及其稳定性研究PDF格式电子书版下载
下载的文件为RAR压缩包。需要使用解压软件进行解压得到PDF格式图书。建议使用BT下载工具Free Download Manager进行下载,简称FDM(免费,没有广告,支持多平台)。本站资源全部打包为BT种子。所以需要使用专业的BT下载软件进行下载。如BitComet qBittorrent uTorrent等BT下载工具。迅雷目前由于本站不是热门资源。不推荐使用!后期资源热门了。安装了迅雷也可以迅雷进行下载!
(文件页数 要大于 标注页数,上中下等多册电子书除外)
注意:本站所有压缩包均有解压码: 点击下载压缩包解压工具
图书目录
第1章 绪论1
1.1 引言1
1.2 淬硬钢精密车削的优点2
1.3 硬态切削机理的国内外研究现状3
1.3.1 锯齿形切屑形成机理4
1.3.2 硬态切削表面完整性的研究5
1.3.3 切削过程有限元模拟技术国内外研究现状8
1.4 车削加工稳定性极限预测的研究现状9
第2章 高速切削技术和硬态切削技术概述13
2.1 高速切削技术13
2.1.1 概念13
2.1.2 理论基础及特点16
2.1.3 高速切削加工的结构体系19
2.1.4 相关技术及其发展现状19
2.2 硬态切削技术34
2.2.1 硬态切削的概念34
2.2.2 硬态切削技术的特点35
2.2.3 高速硬态切削对刀具的要求36
2.2.4 硬态车削的应用与展望40
第3章 机床颤振的基本理论41
3.1 自激振动的基本概念及特点42
3.1.1 相平面、平衡点、极限环及其稳定性42
3.1.2 自激振动的特点45
3.2 速度反馈引起的切削颤振47
3.2.1 切削过程中的速度反馈机理48
3.2.2 速度反馈所形成的负阻尼49
3.2.3 自激振动的能量机理50
3.2.4 能量平衡与振幅稳定性52
3.2.5 颤振的阈限53
3.3 位移延时反馈引起的切削颤振54
3.3.1 位移反馈、负刚度与静态不稳定性54
3.3.2 位移的延时反馈58
3.3.3 金属切削过程中的再生颤振60
3.4 模态耦合引起的切削颤振68
3.4.1 模态耦合与模态耦合系统的稳定性68
3.4.2 金属切削中的模态耦合自激振动71
第4章 淬硬钢高速精密切削加工切屑形成特征研究76
4.1 淬硬钢GCr15切屑形成的切削实验条件77
4.2 精密切削淬硬钢GCr15的锯齿形切屑微观观察77
4.2.1 锯齿形切屑齿顶端面微观形貌77
4.2.2 锯齿形切屑底端面微观形貌77
4.2.3 锯齿形切屑横断面微观观察78
4.2.4 锯齿形切屑断裂面微观形貌79
4.3 淬硬钢精密切削过程绝热剪切行为的有限元模拟与分析80
4.3.1 淬硬钢精密切削过程二维有限元模型的建立80
4.3.2 锯齿形切屑形成过程的有限元模拟结果82
4.4 锯齿形切屑形成过程模型86
4.5 精密切削淬硬钢GCr15的切屑形态研究86
4.5.1 不同切削速度对切屑形态的影响87
4.5.2 不同背吃刀量对切屑形态的影响89
4.5.3 不同进给量对切屑形态的影响91
4.5.4 带状切屑向锯齿形切屑转变的界限92
第5章 硬态切削加工系统稳定性极限预测94
5.1 再生型淬硬钢精密切削系统动力学分析94
5.1.1 淬硬钢的再生型圆弧刃精密切削颤振系统动力学模型94
5.1.2 再生型圆弧刃精密切削系统动力学模型的建立96
5.1.3 淬硬钢精密切削系统稳定性极限分析96
5.2 稳定性极限的数值仿真方法与动力学参数影响分析99
5.2.1 硬态切削系统稳定性极限的数值仿真方法99
5.2.2 切削系统动力学参数对稳定性极限的影响100
5.3 淬硬钢精密切削系统动力学参数的测量102
5.3.1 系统阻尼比的测量103
5.3.2 刚度系数κ的测量104
5.3.3 系统固有频率的测量105
5.3.4 切削刚度系数κc的识别106
5.3.5 方向系数u的识别112
5.3.6 淬硬钢精密切削的稳定性极限预测结果113
5.4 淬硬钢精密切削的稳定性极限预测条件113
5.4.1 不同刀尖圆弧半径的三维稳定性极限预测113
5.4.2 不同进给量的三维稳定性极限预测115
5.5 多参数的稳定性极限预测结果分析116
5.5.1 硬态切削加工中的稳定性极限预测结果影响因素分析116
5.5.2 振动抑制措施的讨论117
第6章 稳定性极限预测的实验考证及切削振动分析118
6.1 淬硬钢精密切削稳定性研究实验切削条件118
6.2 稳定性极限预测的单切削参数法实验考证119
6.2.1 单切削参数法实验验证参数选择119
6.2.2 稳定性极限预测的单切削参数法实验考证结果120
6.2.3 非颤振状态与切削颤振的加工表面形貌120
6.3 稳定性极限预测的变背吃刀量法实验考证121
6.3.1 变背吃刀量法实验原理121
6.3.2 稳定性极限预测的背吃刀量法实验考证结果122
6.3.3 变背吃刀量法非颤振向切削颤振状态转变的加工表面形貌123
6.4 切削振动信号及其谱阵分析124
6.4.1 空载状态到切削稳定状态过渡过程的刀具振动信号特征124
6.4.2 平稳切削状态与切削颤振状态的切削振动信号特征126
6.4.3 动态切削力与振动信号的相关特性分析128
第7章 精密硬态切削加工表面粗糙度与塑性侧流研究130
7.1 淬硬钢切削加工表面塑性侧流的形成机理研究130
7.1.1 淬硬钢切削加工表面塑性侧流三维有限元仿真130
7.1.2 表面塑性侧流形成过程模型与形成机理134
7.2 加工表面塑性侧流程度评判标准的建立134
7.3 淬硬钢切削加工表面侧流数学模型135
7.3.1 塑性侧流凸峰高度数学模型的建立135
7.3.2 圆弧刃与直线刃组合的车削表面残留高度几何数学模型建立137
7.3.3 考虑塑性侧流影响的切削加工表面粗糙度数学模型建立138
7.3.4 塑性侧流凸峰高度及其影响下的表面粗糙度数学模型的讨论138
7.4 表面塑性侧流与表面粗糙度的硬态切削实验研究138
7.4.1 实验条件138
7.4.2 刀尖圆弧半径对表面塑性侧流的影响139
7.4.3 进给量对表面塑性侧流的影响141
7.4.4 精密硬态切削加工表面粗糙度的正交实验优化143
第8章 精密硬态切削的多元非线性回归模型与综合优化146
8.1 精密硬态切削过程的多目标优化实验设计146
8.2 精密硬态切削过程的多元非线性回归综合模型147
8.2.1 表面粗糙度建模147
8.2.2 刀具切削行程建模148
8.2.3 刀具径向振动建模150
8.4 精密硬态切削过程的多目标优化151
8.5 优化结果的实验验证152
参考文献153