图书介绍
中国材料工程大典 第17卷 材料表面工程 下PDF|Epub|txt|kindle电子书版本网盘下载
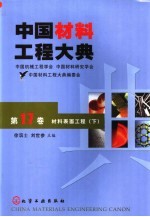
- 徐滨士,刘世参主编;中国机械工程学会,中国材料研究学会,中国材料工程大典编委会编 著
- 出版社: 北京:化学工业出版社
- ISBN:7502573194
- 出版时间:2006
- 标注页数:656页
- 文件大小:102MB
- 文件页数:681页
- 主题词:材料科学;金属表面处理
PDF下载
下载说明
中国材料工程大典 第17卷 材料表面工程 下PDF格式电子书版下载
下载的文件为RAR压缩包。需要使用解压软件进行解压得到PDF格式图书。建议使用BT下载工具Free Download Manager进行下载,简称FDM(免费,没有广告,支持多平台)。本站资源全部打包为BT种子。所以需要使用专业的BT下载软件进行下载。如BitComet qBittorrent uTorrent等BT下载工具。迅雷目前由于本站不是热门资源。不推荐使用!后期资源热门了。安装了迅雷也可以迅雷进行下载!
(文件页数 要大于 标注页数,上中下等多册电子书除外)
注意:本站所有压缩包均有解压码: 点击下载压缩包解压工具
图书目录
第10篇 热浸镀1
第1章 概述3
1.2 镀锌层的形成5
1.1 Fe-Zn二元系相图及镀锌层的相结构5
第2章 热镀锌5
1 热镀锌层的形成5
2.1 钢基化学成分的影响6
2 钢基成分、锌液成分及工艺因素对镀锌层结构和性能的影响6
2.2 锌液成分的影响7
2.3 工艺因素的影响10
3.1 耐蚀性11
3 镀锌钢材的性能11
2.4 钢带表面状态的影响11
4 镀锌钢材的用途13
3.3 焊接性能13
3.2 力学性能13
2 IF钢的特性15
1.4 高强度高深冲性合金化镀锌板的开发15
第3章 汽车用合金化镀锌板15
1 概述15
1.1 汽车用合金化镀锌板性能与镀层相结构15
1.2 热镀锌及合金化过程中Fe-Zn合金相的形成机理15
1.3 热镀锌及合金化处理装备的发展15
3.2 冲压成形时镀层附着性与镀层相结构和铁含量的关系16
3.1 汽车用合金化镀锌板的使用性能及其检测方法16
3 IF钢合金化镀锌板使用性能与镀层相结构和铁含量的关系16
3.3 IF钢合金化镀锌板焊接性与镀层相结构和铁含量的关系20
4.1 高强度超深冲性钢板21
4 高强度合金化镀锌板21
3.4 IF钢合金化镀锌板的最佳铁含量和相结构21
4.2 高强度超深冲性合金化镀锌板的进展22
1.1 铁铝和铁铝硅相图及镀层相结构25
1 热镀铝层的形成25
第4章 热镀铝25
2.1 钢基体化学成分的影响26
2 钢基体及铝液化学成分和热镀铝工艺参数对镀层特性的影响26
1.2 铁与熔融铝的反应及镀铝层的形成26
2.2 铝液化学成分的影响27
2.3 热镀铝工艺参数对镀铝层特性的影响28
3.1 改变钢基体成分29
3 镀铝钢板的发展29
4.2 耐蚀性31
4.1 耐热性31
3.2 改变镀层成分31
4 镀铝钢材的性能31
4.3 对光和热的反射性32
5 镀铝钢材的用途33
4.4 镀铝钢材的加工性和焊接性33
1.3 Zn-Al合金镀层的显微结构34
1.2 镀层成分及第三组分34
第5章 热镀锌铝合金34
1 Zn-Al合金镀层成分及镀层结构34
1.1 Zn-Al二元系相图34
2.1 耐蚀性35
2 Zn-55%Al合金镀层钢板的性能与用途35
2.2 耐热性及对光和热的反射性36
3.3 大气曝晒试验结果37
3.2 SO2加速腐蚀试验结果37
2.3 力学性能及焊接性37
2.4 Zn-55%Al镀层钢板的用途37
3 Zn-5%Al-RE合金镀层钢板的性能和用途37
3.1 盐雾试验结果37
4.2 Zn-0.5%Mg镀层钢板的性能38
4.1 镀层中镁含量的确定38
3.4 Zn-5%Al镀层钢板的用途38
4 Zn-0.5%Mg镀层钢板38
4.4 腐蚀产物的组成和结构39
4.3 Zn-0.5%Mg镀层钢板镀层的结构39
5.3 对Zn-6%Al-3%Mg镀层耐蚀性的评价40
5.2 Zn-6%Al-3%Mg镀层结构40
5 Zn-6%Al-3%Mg镀层钢板40
5.1 镀层成分的确定40
6.1 镀层组成的确定41
6 Zn-11%Al-3%Mg-0.2%Si镀层钢板41
7.1 热镀Zn-Ni及Zn-Ni-Sn-Bi镀层42
7 特殊用途的锌基合金镀层42
6.2 Zn-11%Al-3%Mg-0.2%Si镀层钢板的耐蚀性42
7.2 热镀Zn-Bi合金镀层43
1.2 铅锡合金镀层钢板的性能45
1.1 铅锡合金镀层结构45
第6章 热镀铅锡和锌锡合金45
1 热镀铅锡合金镀层钢板45
2.2 冲压成形性试验46
2.1 耐蚀性试验46
1.3 镀铅钢板的用途46
2 热镀锡锌合金镀层钢板46
2.3 焊接性试验47
6 应用实例48
5 镀层金属及热镀工艺的经济性48
第7章 热浸镀层的选用原则及应用实例48
1 使用介质的腐蚀性48
2 热浸镀层对钢材的防护性48
3 镀层对钢材使用性能的影响48
4 镀层的表观特性48
1.1 氢还原法50
1 热浸镀工艺50
第8章 热浸镀工艺及安全防护50
2.1 氢还原法的安全与防护51
2 热浸镀工艺中的安全与防护51
1.2 熔剂法51
2.2 熔剂法的安全与防护52
参考文献53
第11篇 气相沉积技术及功能薄膜材料制备55
1.1 物质的热蒸发现象57
1 真空蒸镀薄膜制备技术57
第1章 物理气相沉积57
1.2 蒸镀薄膜的厚度均匀性及薄膜的纯度59
1.3 真空蒸发装置61
1.4 真空蒸镀薄膜沉积技术的应用实例64
2 溅射技术66
2.1 气体放电现象与等离子体67
2.2 物质的溅射现象69
2.3 溅射沉积装置72
2.4 溅射薄膜沉积技术的应用实例78
3.1 概述80
3 离子镀技术80
3.2 离子镀的原理和特点81
3.3 活性反应离子镀84
3.5 离化团束离子镀86
3.4 溅射离子镀86
3.7 空心阴极离子镀87
3.6 热阴极离子镀87
3.8 真空电弧离子镀88
3.9 离子镀的综合技术91
1.1 化学气相沉积原理94
1 化学气相沉积(CVD)理论基础94
第2章 化学气相沉积94
1.2 化学气相沉积过程热力学98
1.3 化学气相沉积过程动力学99
1.4 气体输运过程100
2.1 CVD沉积装置设计参数101
2 化学气相沉积装置101
2.2 CVD装置实例103
3.1 化学气相沉积工艺参数对薄膜沉积的影响104
3 化学气相沉积工艺104
3.2 化学气相沉积中的工艺-组织-性能关系105
3.3 化学气相沉积过程测试和监控108
4 化学气相沉积(CVD)类型109
4.2 等离子体增强CVD(PECVD)110
4.1 热激活CVD(TACVD)110
4.3 金属有机化合物化学气相沉积(MOCVD)113
4.4 光辅助CVD(PACVD)117
4.5 原子层外延(ALE)118
4.6 气溶胶辅助化学气相沉积(AACVD)119
4.8 化学气相渗透(CVI)120
4.7 火焰辅助化学气相沉积(FACVD)120
4.9 电化学气相沉积121
5.1 金属薄膜122
5 材料的化学气相沉积122
5.2 非金属薄膜125
5.3 陶瓷薄膜127
5.4 Ⅲ-Ⅴ族和Ⅱ-Ⅵ族化合物130
1.1 硬质膜的种类和性质132
1 硬质薄膜和装饰性硬质薄膜132
第3章 薄膜材料的制备及应用132
1.2 硬质薄膜的制备、性能与应用133
1.3 硬质装饰涂层137
1.4 超硬薄膜的性质和应用140
2.1 超导薄膜144
2 电磁功能薄膜的制备和应用144
2.2 压电与铁电薄膜147
2.3 磁性薄膜149
3.1 介电薄膜151
3 微电子与光电子薄膜的制备和应用151
3.2 半导体薄膜153
3.3 导电薄膜154
3.4 电阻薄膜155
3.7 透明导电薄膜157
3.6 光电导薄膜157
3.5 光生伏特薄膜157
3.8 发光薄膜158
4.1 基本光学薄膜159
4 光学薄膜与集成光学薄膜159
4.2 控光薄膜162
4.3 光波导薄膜166
4.4 光开关薄膜167
5.1 化学气相沉积金刚石膜168
5 金刚石膜168
4.5 光调制薄膜168
5.2 化学气相沉积金刚石膜的工业化应用173
5.4 金刚石膜发展趋势182
5.3 金刚石膜的质量控制与监测182
1.2 微电子机械系统及微电子机械系统(MEMS)器件183
1.1 集成铁电器件183
第4章 功能薄膜材料发展趋势183
1 功能薄膜材料的小型化、多功能和高集成183
4 超硬薄膜的进展184
3 兰格缪尔-布洛奇特薄膜184
2 信息功能薄膜材料184
6.1 功能薄膜制备技术的发展185
6 功能薄膜制备技术发展趋势185
5 功能薄膜异质结构185
6.3 功能薄膜材料制备过程诊断和原位实时监控186
6.2 功能薄膜表征技术的发展186
7 快速原型化187
1.1 薄膜制备技术的分类188
1 薄膜气相沉积技术的选用原则188
第5章 气相沉积技术选用原则及应用实例188
1.3 薄膜制备技术的选用原则190
1.2 薄膜材料的应用领域190
2.1 薄膜沉积技术在半导体工业中的应用192
2 薄膜沉积技术应用实例192
2.2 硬质合金工具涂层194
1.2 处理装置的选定198
1.1 总体方案的确定198
第6章 气相沉积工艺的安全与防护198
1 工业有害气体处理的原则198
4 气相沉积设备的腐蚀和防护199
3 气相沉积中工件(衬底)清洗中的有机溶剂199
2 气相沉积中使用的有害气体及防护199
参考文献200
第12篇 高能束表面处理技术207
2.2 高能束表面处理技术的特点209
2.1 高能束表面处理技术209
第1章 概述209
1 高能束表面处理的能源209
2 高能束表面处理技术及其特点209
2.3 高能束表面处理技术的比较210
2.3 电子的加速212
2.2 热电子发射212
第2章 电子束表面处理技术212
1 电子束表面处理技术主要特点212
2 电子束与材料的相互作用212
2.1 电子发射212
2.6 电子束和材料相互作用机理213
2.5 真空213
2.4 电子束的控制213
2.8 加热和冷却速率215
2.7 电子束加热的效率215
3.2 电子束加热器的设计216
3.1 电子枪216
3 电子束表面处理装置216
3.3 电子束的类型和加工的轨迹形状217
4 电子束表面处理方法及工艺218
4.1 电子束热处理技术219
4.2 电子束重熔技术222
5 电子束表面处理的应用223
4.3 蒸发技术223
1.1 等离子体和离子束注入225
1 离子束表面处理技术及特点225
第3章 离子束表面处理技术225
2.1 连续的离子束注入226
2 离子束与材料的相互作用226
1.2 离子束注入的特点226
3.1 连续离子束注入机229
3 离子注入设备229
2.2 脉冲离子束注入229
3.2 脉冲离子注入机232
4 离子束注入工艺234
5 离子注入材料性能的改变235
5.1 被注入材料的摩擦性能236
5.4 被注入材料的耐蚀性239
5.3 被注入材料的硬度及附着力239
5.2 被注入材料的强度239
6 离子注入技术的应用241
5.5 被注入材料的其他性能241
1 激光表面处理的分类243
第4章 激光表面处理技术243
2.1 材料对激光的反射与吸收244
2 激光与材料相互作用244
2.2 表面状态对金属光学特性的影响245
2.4 反常吸收效应246
2.3 金属吸收率随温度的变化246
2.6 激光诱导等离子体247
2.5 金属的激光加热247
3.1 激光器249
3 激光表面处理系统249
3.3 填充材料的输送系统275
3.4 激光熔覆的控制系统279
4.1 激光表面淬火281
4 激光表面处理工艺281
4.2 激光表面重熔286
4.3 激光表面合金化289
4.4 激光表面熔覆295
4.5 激光表面非晶化299
4.6 激光表面冲击强化301
4.7 激光表面清洗304
4.8 激光化学气相沉积(LCVD)305
4.9 激光表面烧蚀310
4.10 激光表面处理应用312
5 激光加工安全防护316
5.1 激光加工环境中可能的危害316
5.3 防护器具319
5.2 强制性安全标准319
5.4 管理条例与防护操作320
参考文献321
第13篇 纳米表面工程327
1.3 界面与表面效应329
2 纳米表面工程的内涵329
1.2 量子尺寸效应329
第1章 概述329
1 纳米材料的特性329
1.1 小尺寸效应329
4 实用纳米表面工程技术330
3 纳米化表层的四条途径330
5 纳米表面工程的优越性331
2.2 液体介质中纳米颗粒的存在行为332
2.1 纳米颗粒团聚的原因332
2 纳米颗粒的团聚与分散332
第2章 纳米颗粒的表面改性332
1 概述332
2.3 改善液体介质中纳米颗粒分散性的途径333
3.1 纳米颗粒表面物理改性334
3.2 纳米颗粒表面化学改性334
3 纳米颗粒表面改性方法334
3.4 沉淀反应改性335
3.5 胶囊化改性335
3.3 机械/化学复合改性335
4.1 纳米TiO2颗粒的表面改性336
4 纳米颗粒表面改性技术应用实例336
3.6 高能表面改性336
4.2 纳米SiO2颗粒的表面改性337
4.3 纳米CaCO3颗粒的表面改性338
4.4 其他纳米颗粒的表面改性338
2.2 纳米不溶性固体颗粒的选择原则341
2.3 纳米复合电刷镀溶液的配制工艺341
2.1 对纳米复合电刷镀溶液的要求341
第3章 纳米复合电刷镀技术341
1 纳米复合电刷镀技术概述341
2 纳米复合电刷镀溶液341
2.5 纳米复合电刷镀溶液的性能342
2.6 常用纳米复合电刷镀溶液体系342
2.4 纳米复合电刷镀溶液的特点342
3 纳米复合电刷镀层的组织与成形机理343
3.1 纳米复合电刷镀层的组织343
3.2 纳米复合电刷镀层的成形机理344
3.3 纳米复合镀层的性能345
3.4 纳米复合镀层的结合机理346
3.5 纳米复合镀层的强化机理347
4.1 纳米复合电刷镀的一般工艺过程348
4.2 纳米复合电刷镀工艺参数选择348
4 纳米复合电刷镀工艺348
5.1 纳米复合镀技术的应用范围349
5.2 纳米复合电刷镀技术展望349
5 纳米复合电刷镀技术的应用349
1.2 热喷涂技术的应用特点350
1.3 热喷涂技术的工艺流程350
1.1 热喷涂技术及其分类350
第4章 微/纳米热喷涂技术350
1 概述350
2.1 制备方法351
2 热喷涂纳米结构颗粒喂料的制备351
1.4 微/纳米热喷涂351
2.2 实例:Al2O3-TiO2纳米结构颗粒喂料352
3.1 等离子喷涂纳米结构涂层353
3 等离子喷涂技术制备微/纳米结构涂层353
3.2 国内外纳米材料等离子喷涂研究状况355
5 电弧喷涂微/纳米结构涂层356
4 超音速火焰喷涂制备微/纳米结构涂层356
6 微/纳米热喷涂技术的应用前景357
3 涂料用纳米颗粒填料及在树脂中的分散问题358
3.1 纳米颗粒填料358
2.3 纳米颗粒填充复合功能涂料358
第5章 纳米复合功能涂料技术358
1 功能涂料基本概念358
2 纳米复合功能涂料358
2.1 纳米改性涂料358
2.2 纳米结构涂料358
4 涂料制备设备359
5 涂料结构及性能表征359
3.2 纳米颗粒填料在树脂中的分散技术359
6 纳米复合功能涂料应用360
6.1 纳米复合抗紫外线涂料360
6.4 纳米复合抗静电涂料361
6.5 纳米复合抗菌防污涂料361
6.3 纳米复合电磁涂料361
6.2 纳米复合热障涂料361
7.2 纳米复合界面涂料362
7.3 纳米复合高强度涂料362
7.1 纳米复合激光涂料362
6.6 纳米复合透明耐磨涂料362
6.7 纳米复合阻燃涂料362
7 纳米复合功能涂料研究进展362
1.2 润滑膜增强机制364
1.3 填充条件修复作用机制364
1.1 沉积膜作用机制364
第6章 纳米润滑材料364
1 纳米润滑材料的摩擦学作用机理364
2.1 单质纳米粉体的摩擦学性能365
2 纳米润滑材料的主要分类及摩擦学性能365
1.6 表面自修复作用机理365
1.4 表面优化作用机制365
1.5 光滑或超光滑表面滚动摩擦作用机制365
2.2 纳米硫属化合物的摩擦学性能366
2.4 纳米氧化物和氢氧化物的摩擦学性能367
2.3 纳米硼酸盐的摩擦学性能367
2.5 纳米稀土化合物的摩擦学性能368
2.7 矿物微粉的磨损自修复功能369
3 纳米润滑材料的应用369
2.6 高分子纳米微球的摩擦学性能369
3 纳米固体润滑系统的组成及其摩擦学设计原则371
3.1 纳米固体润滑系统的组成371
2 纳米固体润滑技术分类371
第7章 纳米固体润滑技术371
1 纳米固体润滑技术的产生前景371
3.2 摩擦学设计原则372
4 纳米固体润滑组元的制备方法374
5.1 LB膜375
5.2 SAMs膜375
5 润滑特性分子有序膜和高分子聚合物超薄膜的自组装375
5.3 MD膜377
5.4 高分子聚合物超薄膜377
6 纳米固体润滑/耐磨超薄膜378
6.1 纳米固体润滑单层膜378
6.3 纳米润滑/耐磨多层叠膜380
7 超固体润滑膜380
6.2 纳米固体润滑/耐磨多层膜380
7.2 超润滑的实现条件381
7.3 MEMS中的摩擦问题381
7.1 超固体润滑发展现状381
7.4 超固体润滑在MEMS装置中的应用前景382
8 金属基原位加工的纳米润滑/耐磨涂层382
9.1 高分子基纳米润滑/耐磨涂层383
9 非金属基纳米润滑/耐磨涂层383
9.2 陶瓷基纳米耐磨涂层385
1 粘接粘涂技术的组成及形成机理386
1.1 粘接涂层的组成386
第8章 纳米粘接粘涂技术386
2.1 环氧树脂胶黏剂387
2 有机胶黏剂的主要分类以及基本性能387
1.3 粘接剂产生粘接力的基本理论387
1.2 粘接剂与被粘表面产生粘接力的过程387
2.2 酚醛树脂胶黏剂393
2.3 聚氨酯胶黏剂394
2.4 有机硅树脂胶黏剂394
4 纳米胶黏剂395
4.1 纳米有机胶黏剂的制备方法395
3.2 硅酸盐型无机胶黏剂395
3 无机胶黏剂395
3.1 磷酸盐型无机胶黏剂395
5 被粘材料的粘接工艺及常见缺陷的处理396
5.1 被粘材料的粘接工艺396
4.2 纳米粒子对有机胶黏剂性能的影响396
5.2 纳米胶黏剂应用实例397
5.3 常见缺陷的处理方法398
1.2 纳米多层膜的分类399
1.3 典型的纳米多层膜体系以及对超硬性起源的各种探讨399
1.1 纳米多层膜的制备方法399
第9章 纳米硬膜技术399
1 纳米多层膜(纳米超点阵膜)399
2.2 纳米复合涂层体系的分类401
2.3 典型的纳米复合涂层体系401
2.1 沉积纳米复合涂层的方法401
2 纳米复合膜401
2.5 超硬纳米复合涂层的结构404
2.4 超硬纳米复合涂层高硬度、高弹性恢复以及高断裂韧度的起源404
2.6 硬及超硬纳米复合涂层的力学性能405
3.1 TiN/Si3N4纳米超硬复合薄膜的沉积制备406
3 典型纳米硬膜的制备工艺406
3.2 WC-Ti(l-x)AlxN纳米超晶格薄膜的沉积制备407
1 表面自身纳米化的基本原理与制备方法409
1.1 表面机械处理法409
第10章 金属材料的表面自身纳米化409
2.2 形变机制410
2.3 影响塑性变形的因素410
2.1 形变组织410
1.2 非平衡热力学法410
2 微观变形方式410
3.2 表面纳米化的组织演变412
3.1 表面纳米化的结构特征412
3 组织结构特征412
3.3 表面纳米化的微观机理418
4.1 表面性能420
4 表面纳米化对性能的影响420
4.2 整体性能422
5 表面纳米化加工与化学热处理423
5.1 纯铁的气体渗氮423
5.2 38CrMoAl钢的气体渗氮424
6 表面纳米化的应用前景426
参考文献428
第14篇 封存与包装433
2 封存与包装原理435
2.1 影响金属制品锈蚀的原因435
1.2 封存包装的重要性435
第1章 概述435
1 封存与包装的意义435
1.1 含义435
3.2 防锈封存包装的等级436
3.1 技术要求436
3 封存包装技术436
2.2 防锈技术436
3.3 防锈封存包装方法437
1 水溶性防锈封存材料441
1.1 防锈作用原理441
第2章 封存材料441
1.2 选用原则442
1.3 分类及主要品种442
1.4 典型配方及配制工艺444
1.5 国外材料的种类、性能445
2 油脂类防锈材料446
2.1 防锈作用原理446
2.2 防锈油脂选用原则447
2.3 防锈油脂的种类及品种447
2.4 典型配方及配制工艺451
3.2 激光的光学变换与传输系统454
2.5 国外防锈油脂459
3.2 选用原则461
3.1 防锈作用原理461
3 气相防锈封存材料461
3.3 分类及主要品种462
3.5 国外材料的种类、性能465
3.4 典型配方及配制工艺465
4.2 选用原则468
4.1 防锈作用原理468
4 高分子防锈封存材料468
4.3 分类及主要品种469
4.4 典型配方及制备工艺475
1.2 机械零部件防锈封存工艺实施要点482
1.1 防锈工艺的一般技术要求482
第3章 典型机械零部件防锈封存工艺482
1 机械零部件通用防锈封存工艺要点482
2 典型机械制品的防锈封存工艺483
2.1 轴承防锈484
2.2 大型机械防锈封存与包装485
2.4 光学仪器防锈封存与包装486
2.3 刃具与量具防锈封存与包装486
2.5 机械配件的防锈封存与包装487
2.7 露天存放产品防锈封存与包装488
2.6 库存产品的防锈封存与包装488
2 干燥空气封存防锈490
1 充氮封存防锈490
第4章 环境防锈封存490
2.2 干燥剂用量计算491
2.1 干燥剂的选用491
2.3 包装吸湿性产品的防潮性计算493
3.2 除氧包装材料494
3.1 概述494
2.4 干燥空气封存分类494
3 除氧封存494
3.3 除氧封存包装方法495
4.1 测量与控制仪表的选择496
4 环境监控防锈496
4.3 温湿度控制系统497
4.2 执行机构的选择497
参考文献498
第15篇 表面工程技术设计499
1.1 适应性原则501
1 表面技术设计与选择的一般原则501
第1章 概述501
2 表面强化工艺规程的编制502
1.3 经济性原则502
1.2 耐久性原则502
1.1 堆焊方法的选择原则505
1 堆焊技术的设计与选择505
第2章 表面覆层技术的设计与选择505
2.2 热喷涂材料的选择原则507
2.1 热喷涂方法的选择原则507
1.2 堆焊材料的选择原则507
2 热喷涂技术的设计与选择507
3.1 镀敷技术的选择原则508
3 镀敷技术的设计与选择508
3.2 镀层的设计与选择510
4 涂装技术的设计与选择519
4.1 涂层体系的设计和涂料的选择原则519
4.2 涂装工艺的选择原则520
1.2 复合表面技术设计与选择原则522
1.1 概述522
第3章 复合表面技术的设计与选择522
1 复合表面技术设计与选择原则522
2.1 电镀、化学镀复合材料523
2 以增强耐磨性为主的复合表面技术523
2.2 多层涂层527
2.4 含表面热处理的复合强化层529
2.3 功能梯度涂层529
2.5 含激光处理的复合强化层534
3.1 耐蚀复合镀层537
3 以增强耐蚀性为主的复合表面技术537
2.6 其他表面技术的复合537
3.3 镍镉扩散镀层538
3.2 多层镍-铬镀层538
3.4 金属-非金属复合涂层539
3.5 有机复合膜层541
3.6 自蔓延技术制备钢基陶瓷复合材料542
3.7 耐高温热腐蚀复合涂层543
4.1 概述546
4 以增强固体润滑性为主的复合表面技术546
4.2 复合镀固体润滑材料547
4.3 气相沉积复合膜和多层膜548
4.4 含扩渗处理的表面膜层550
4.5 金属塑料复合材料551
4.6 粘结固体润滑膜552
1.3 设备磨损的度量556
1.2 设备的无形磨损556
第4章 表面工程技术经济分析556
1 设备的磨损及其补偿556
1.1 设备的有形磨损556
1.6 表面工程和再制造工程对补偿设备磨损的作用557
1.5 设备的寿命557
1.4 设备磨损的补偿557
2.1 技术经济分析的基本要素558
2 技术经济的基本原理558
2.3 资金的时间价值561
2.2 可比原则561
3.1 静态评价方法564
3 技术经济评价的基本方法564
3.2 动态投资评价法565
4.1 设备大修的经济界限566
4 设备修理、改造与更新的技术经济分析566
3.3 其他效益型指标评价法566
4.3 设备更新方案的评价与选择567
4.2 设备经济寿命的确定567
参考文献570
第16篇 表面工程质量控制与检测571
1.1 表面缺陷的类型及其特征573
1 涂覆层表面缺陷及外观质量检测573
第1章 涂覆层的外观质量检测573
2.3 光度计测量法574
2.2 样板对照法574
1.2 检测条件574
1.3 检测方法574
2 涂覆层表面光泽度的检测574
2.1 目测评定法574
1.2 制样575
1.1 取样575
第2章 涂覆层组织及表面微观形貌的光学显微分析575
1 光学显微分析样品的制备575
2.2 常用测量方法582
2.1 定量金相的常用符号及基本公式582
2 定量金相分析582
2.4 定量金相数据的统计分析583
2.3 定量金相计算公式及其应用583
2.5 自动图像分析仪584
1.1 透射电子显微镜的样品制备585
1 透射电子显微分析585
第3章 涂覆层组织及表面形貌的电子显微分析585
1.2 透射电镜成像操作及像衬度586
1.3 透射电镜在显微分析中的应用587
3.2 扫描隧道显微镜(STM)分析588
3.1 扫描透射电镜(STEM)分析588
2 扫描电子显微镜在显微组织分析中的应用588
3 其他电子(离子)显微分析方法588
3.4 场发射显微镜分析589
3.3 原子力显微镜分析589
3.6 原子探针—场离子显微镜(AP-FIM)590
3.5 场离子显微镜(TFIM)分析590
第4章 涂覆层的晶体及分子结构分析检测591
1.1 X射线衍射的基本原理593
1 X射线衍射结构分析方法593
1.2 X射线衍射分析的应用595
2.1 概述596
2 电子衍射结构分析方法596
2.4 单晶电子衍射花样及其标定597
2.3 多晶电子衍射花样及其标定597
2.2 电子衍射的基本原理597
2.5 样品制备及其他问题598
第5章 涂覆层及其表面的成分分析检测599
第6章 涂覆层表面粗糙度的检测601
1 样板对照法检测602
3 干涉显微镜法603
2 轮廓仪法(触针法)检测603
5 显微镜调焦法604
4 散斑法604
6 扫描隧道显微镜法605
1 滤纸法606
第7章 涂覆层的孔隙率检测606
3 浮力法607
2 涂膏法607
5 孔隙率的其他测定方法608
4 直接称量法608
第8章 涂覆层的硬度检测609
1.2 洛氏硬度试验法610
1.1 布氏硬度试验法610
1 宏观硬度检测610
1.3 维氏硬度检测611
2.1 微观硬度检测方法612
2 微观硬度检测612
2.2 显微硬度测量仪器613
2.3 显微硬度测量中的几个重要问题614
2.4 显微硬度的间接检测法615
3.1 压痕测试原理616
3 纳米涂覆层硬度检测616
3.2 压痕的测量617
3.3 纳米划痕硬度618
1.2 涂覆层厚度测量方法的种类与特点619
1.1 涂覆层厚度的定义619
第9章 涂覆层的厚度检测619
1 概述619
2.1 检测样品制备620
2 光学金相显微镜检测法620
1.3 涂覆层厚度测量方法的选择620
3.2 测量要点621
3.1 样品制备621
2.2 检测方法621
3 扫描电子显微镜检测621
5.1 磁性法涂覆层厚度检测622
5 测厚仪法检测622
4 射线法检测622
4.1 X射线荧光测厚法622
4.2 β射线反(背)散射测厚法622
5.2 涡流法涂覆层厚度检测623
7.2 计时液流法624
7.1 点滴法624
6 软廓仪(触针)法检测624
7 化学溶解法检测624
7.3 溶解法626
7.4 阳极溶解库仑法627
9.1 微量天平法628
9 纳米薄膜厚度的精密测量方法628
8 光干涉法检测628
8.1 测量原理628
8.2 样品制备628
8.3 膜厚的测定628
10.3 电容法629
10.2 微波法629
9.2 石英振子法629
10 涂覆厚度的其他检测方法629
10.1 椭圆偏振法629
1 对涂覆层和基体直接加载法630
第10章 涂覆层与基体结合强度的检验630
2.1 直接拉伸试验法631
2 使用黏结剂的检验方法631
2.4 拉导剥离法632
2.3 抗剪强度检测法632
2.2 改进的直接拉伸检测法632
3.1 划痕法633
3 涂覆层局部变形法633
2.5 扭矩法633
3.2 压痕法634
5.1 冲击试验法635
5 其他测量方法635
3.3 刮剥法635
3.4 动态拉伸法635
4 基片变形法635
4.1 弯曲法635
4.2 基体拉伸法635
5.9 X射线法636
5.8 电磁力法636
5.2 杯突试验法636
5.3 热振试验法636
5.4 超离心力法636
5.5 超声波法636
5.6 冲击波法636
5.7 磨损法636
第11章 涂覆层耐蚀性能的检测637
1.1 中性盐雾试验(NSS)638
1 盐雾试验法检测638
1.2 铜盐加速醋酸盐雾试验(CASS)640
2.3 试验结果评定641
2.2 测试方法641
2 湿热试验641
2.1 测试设备技术参数641
4.3 测试条件642
4.2 测试设备642
3 腐蚀膏试验642
3.1 方法原理642
3.2 腐蚀膏的制备642
3.3 试验方法642
3.4 试验结果评定642
4 二氧化硫工业气体腐蚀试验642
4.1 方法原理642
5.2 测试溶液和补给溶液643
5.1 测试设备643
4.4 试验方法643
4.5 试验结果评定643
4.6 二氧化硫气体的制备和分析643
5 周期浸润腐蚀试验643
6.1 大气条件分类644
6 大气暴露腐蚀试验法检测644
5.3 试样644
5.4 试验周期644
5.5 试验结果的检查与评定644
6.5 试验结果的定性评定645
6.4 试样的要求和暴露方法645
6.2 暴露方式645
6.3 大气暴露场的选择和要求645
7.1 电解腐蚀试验646
7 其他人工加速腐蚀试验646
6.6 试样暴露结果的定量评定646
7.4 硫代乙烯胺腐蚀试验647
7.3 硫化氢试验647
7.2 全浸腐蚀试验647
2 弯曲率检验法649
1 挠度法649
第12章 涂覆层残余应力的检测649
5 X射线分析法检测650
4 电阻应变法650
3 螺旋收缩仪法650
6 涂覆层残余应力的其他检测651
1 磨损试验方法652
第13章 涂覆层耐磨性能的检测652
2 耐磨性的评价653
2 涂层的绝热性654
1 涂层的耐热性654
第14章 涂覆层其他性能的检测654
参考文献656