图书介绍
实用热处理手册PDF|Epub|txt|kindle电子书版本网盘下载
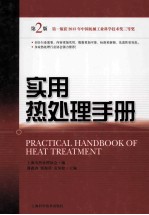
- 上海市热处理协会编著 著
- 出版社: 上海:上海科学技术出版社
- ISBN:9787547819456
- 出版时间:2014
- 标注页数:815页
- 文件大小:428MB
- 文件页数:837页
- 主题词:热处理-技术手册
PDF下载
下载说明
实用热处理手册PDF格式电子书版下载
下载的文件为RAR压缩包。需要使用解压软件进行解压得到PDF格式图书。建议使用BT下载工具Free Download Manager进行下载,简称FDM(免费,没有广告,支持多平台)。本站资源全部打包为BT种子。所以需要使用专业的BT下载软件进行下载。如BitComet qBittorrent uTorrent等BT下载工具。迅雷目前由于本站不是热门资源。不推荐使用!后期资源热门了。安装了迅雷也可以迅雷进行下载!
(文件页数 要大于 标注页数,上中下等多册电子书除外)
注意:本站所有压缩包均有解压码: 点击下载压缩包解压工具
图书目录
第一章 金属材料及热处理基础1
第一节 钢的热处理基础知识1
一、铁碳合金相图1
(一)Fe-Fe3 C及Fe-C合金相图的结构2
(二)Fe-Fe3 C及Fe-C合金相图中重要的点和线2
二、合金元素在钢中的作用5
(一)合金元素与铁和碳的作用及其在钢中的分布5
(二)合金元素对Fe-Fe3 C相图的影响7
(三)合金元素对钢的相变和热处理的影响8
(四)合金元素对过冷奥氏体转变的影响9
(五)合金元素对淬火钢回火转变的影响9
(六)非调质机械结构钢中的微合金元素10
三、钢的热处理原理10
(一)钢在加热过程的组织转变10
(二)钢的过冷奥氏体转变10
四、钢铁的常规热处理工艺12
(一)钢铁零件的退火12
(二)钢铁零件的正火处理16
(三)钢铁零件退火、正火常见缺陷17
(四)钢的淬火17
(五)钢在回火时的转变24
(六)钢的冷处理27
五、金属材料的性能与材料的选择28
六、钢的生产加工过程对钢组织和性能的影响31
(一)冶炼过程对钢组织和性能的影响31
(二)铸造过程对钢组织和性能的影响37
(三)压力加工过程对钢组织和性能的影响39
(四)焊接对钢组织和性能的影响43
(五)零件设计、机械加工对热处理的影响43
第二节 碳钢、易切削钢、铸钢的牌号、临界点、性能与热处理工艺48
一、碳钢的分类、性能及常用热处理方法48
二、碳素结构钢的牌号、临界点、性能与热处理工艺49
三、碳素工具钢的牌号、临界点、性能与热处理工艺52
四、易切削结构钢的牌号、类型与两种状态下的纵向力学性能52
五、工程用铸钢的牌号、性能与热处理工艺54
第三节 合金结构钢的牌号、临界点、性能与热处理工艺61
一、合金钢的分类61
二、合金结构钢的牌号、临界点与热处理工艺62
三、低合金高强度结构钢的牌号与性能66
四、弹簧钢的牌号、临界点、性能与热处理工艺68
五、轴承用钢的牌号、临界点、性能与热处理工艺68
六、非调质机械结构钢的牌号与性能71
第四节 合金工具钢的牌号、临界点、性能与热处理工艺72
一、高速工具钢的牌号、临界点、性能与热处理工艺72
二、冷作模具钢的牌号、临界点、性能与热处理工艺72
三、热作模具钢的牌号、临界点、性能与热处理工艺72
四、塑料模具钢的牌号、临界点、性能与热处理工艺72
五、量具刃具用钢的牌号、临界点、性能与热处理工艺72
六、耐冲击工具用钢的牌号、临界点、性能与热处理工艺72
七、无磁模具钢的牌号、临界点、性能与热处理工艺72
八、部分美国工具钢的淬火-回火参考工艺规范72
九、部分美国高速钢的淬火-回火参考工艺规范72
第五节 特殊性能钢的牌号、性能与热处理工艺79
一、不锈钢的性能与热处理工艺79
二、耐热钢的性能与热处理工艺85
三、耐磨钢的水韧处理87
四、核电装备用材料与热处理工艺88
五、高温合金的牌号与热处理工艺89
(一)高温合金牌号命名法91
(二)铁基变形高温合金的热处理工艺91
(三)镍基变形高温合金的热处理工艺94
(四)铸造高温合金的热处理工艺97
第六节 铸铁的牌号、性能与热处理工艺99
一、灰铸铁99
(一)灰铸铁的牌号与性能99
(二)灰铸铁的热处理工艺101
二、球墨铸铁103
(一)球墨铸铁的牌号与性能103
(二)球墨铸铁的热处理工艺106
三、可锻铸铁108
(一)可锻铸铁的牌号与性能108
(二)可锻铸铁的热处理工艺109
四、蠕墨铸铁110
五、耐磨铸铁110
六、抗磨铸铁111
七、耐热铸铁112
八、高硅耐蚀铸铁112
第七节 有色金属的牌号、性能与热处理工艺113
一、铝及铝合金113
(一)铝的性能113
(二)工业纯铝的牌号及化学成分113
(三)变形铝合金114
(四)铸造铝合金127
(五)铝合金热处理常见缺陷及预防对策131
二、铜及铜合金131
(一)纯铜131
(二)铜合金132
三、镁及镁合金143
四、钛及钛合金148
(一)钛及钛合金的牌号及化学成分149
(二)钛及钛合金的热处理152
(三)钛合金的热氢处理158
五、形状记忆合金159
六、膨胀合金161
第八节 铁基粉末冶金材料的牌号、性能与热处理工艺163
一、铁基粉末冶金材料的牌号和特点163
二、铁基粉末冶金材料的标记方法164
三、铁基粉末冶金件的制造工艺流程166
四、粉末冶金材料的热处理166
第二章 真空热处理167
第一节 真空获得技术、真空测量和真空检漏167
一、真空基本知识167
二、真空获得技术168
(一)真空热处理炉常用的真空泵168
(二)真空系统169
(三)真空系统的主要附件171
三、真空测量172
四、真空检漏173
第二节 真空热处理工艺176
一、真空热处理工艺原理176
二、真空热处理加热工艺参数的确定178
三、真空热处理的冷却方法181
(一)真空油淬181
(二)真空气淬183
(三)其他冷却方法189
四、真空气淬热处理技术的发展动向189
五、真空热处理工艺192
(一)真空退火192
(二)真空淬火、真空回火195
六、真空渗碳210
(一)常规的真空渗碳210
(二)低压真空渗碳212
(三)AvaC乙炔低压渗碳215
(四)真空渗碳的发展217
第三节 真空热处理炉217
一、真空热处理炉的分类及功率确定217
二、真空热处理炉的主要结构219
(一)炉壳219
(二)加热器219
(三)隔热屏222
(四)真空隔热闸门224
三、常用真空热处理炉简介225
(一)外热式真空热处理炉225
(二)内热式真空热处理炉225
(三)抽空炉234
(四)真空回火炉235
(五)真空退火炉236
四、真空热处理炉的辅助设施236
(一)真空热处理炉循环水冷却系统236
(二)氮气供给系统240
五、真空热处理炉的选用、保养及其他240
(一)真空热处理炉的选用原则240
(二)真空热处理炉的基本技术指标241
(三)真空热处理炉的性能试验方法241
(四)真空热处理炉的验收工作242
(五)真空热处理炉的保养技术243
第三章 表面改性热处理245
第一节 表面加热淬火245
一、火焰淬火245
二、脉冲淬火248
第二节 钢的渗碳250
一、概述250
二、固体渗碳250
三、气体渗碳251
四、渗碳后的热处理260
五、渗碳工艺的发展261
(一)高温渗碳261
(二)深层渗碳263
(三)高浓度渗碳(碳氮共渗)263
(四)真空渗碳264
六、渗碳件的常见缺陷、产生原因及防止措施264
第三节 钢的渗氮266
一、基本概念267
二、常用渗氮钢及其预备热处理269
三、气体渗氮270
(一)工件渗氮前的准备工作270
(二)气体渗氮工艺271
(三)典型工件应用实例272
四、离子渗氮274
(一)工件渗氮前的准备工作274
(二)离子渗氮工艺274
(三)典型工件应用实例276
五、渗氮工艺的发展277
(一)活性屏离子渗氮277
(二)不锈钢固溶渗氮(真空渗氮)278
(三)不锈钢的低温渗氮和渗碳280
六、渗氮件的常见缺陷、产生原因及防止措施283
第四节 碳氮共渗与氮碳共渗285
一、气体碳氮共渗285
(一)气体碳氮共渗前的准备工作285
(二)气体碳氮共渗工艺285
(三)典型工件应用实例287
(四)碳氮共渗用钢及共渗后的热处理288
(五)碳氮共渗件的常见缺陷、产生原因及防止措施288
二、气体氮碳共渗289
(一)气体氮碳共渗前的准备工作289
(二)气体氮碳共渗工艺290
(三)应用实例291
(四)气体氮碳共渗件的常见缺陷、产生原因及防止措施292
三、液体氮碳共渗293
(一)液体氮碳共渗前的准备工作293
(二)液体氮碳共渗工艺293
(三)氮碳共渗用钢及共渗后的性能295
(四)液体氮碳共渗的常见缺陷、产生原因及防止措施296
第五节 激光热处理296
一、激光发生器297
二、激光加热金属的特点300
三、激光淬火301
(一)激光淬火的适用钢材和铸铁301
(二)激光淬火前的准备工作301
(三)激光淬火工艺302
(四)应用实例302
第六节 气相沉积表面改性303
一、概述303
二、物理气相沉积技术304
(一)真空蒸发镀305
(二)溅射镀306
(三)离子镀309
三、化学气相沉积311
(一)CVD中的化学反应312
(二)CVD常用的硬质涂层方法314
(三)其他方法316
四、气相沉积技术的应用和发展317
(一)气相沉积硬质涂层318
(二)CVD涂层工具钢的热处理319
第四章 感应热处理321
第一节 感应加热原理321
一、电磁感应321
二、表面效应(集肤效应)321
三、邻近效应322
四、圆环效应322
五、导磁体槽口效应322
六、尖角效应322
第二节 感应热处理工艺322
一、硬化层深度322
二、电流频率322
三、功率324
四、加热方法和冷却方式329
五、感应淬火温度330
六、冷却方法和冷却介质332
七、感应淬火件的回火333
八、工件感应淬火硬化区域的合理分布335
第三节 感应器的选用和设计制作336
一、工频感应器设计337
二、中高频感应器设计338
三、常用中高频感应器举例340
第四节 感应热处理设备344
一、高频感应加热电源装置344
二、中频感应加热电源装置346
三、超音频感应加热电源装置347
四、工频感应加热电源装置348
五、感应淬火机床348
(一)淬火机床的选择348
(二)常用感应淬火机床规格349
第五节 感应热处理件的常见缺陷及预防措施351
第五章 控制(可控)气氛热处理353
第一节 控制气氛基础知识353
一、几个物理量及相关定律353
二、气氛的主要组成356
三、炉内气氛的气体反应357
四、气氛的碳势358
第二节 常用热处理气氛及其获得361
一、常用热处理气氛361
二、制备气氛的主要原料362
三、常用气氛的制备365
四、气氛的分析测量和仪器设备369
第三节 控制气氛热处理炉372
一、控制气氛热处理炉的特性和基本要求372
二、常用控制气氛热处理炉372
第四节 控制气氛热处理操作的安全378
一、预防火灾和爆炸378
二、预防窒息和中毒379
三、车间安全生产指南381
第六章 淬火冷却和冷却介质382
第一节 钢的过冷奥氏体冷却转变382
一、过冷奥氏体等温冷却转变382
二、过冷奥氏体连续冷却转变384
三、钢的过冷奥氏体冷却曲线386
第二节 淬硬性和淬透性401
一、淬硬性401
二、淬透性401
三、影响淬透性的因素416
第三节 淬火冷却烈度和淬透层深度418
一、淬火冷却烈度418
二、淬透层深度(淬硬层厚度)419
第四节 淬火冷却介质的选择与检测420
一、淬火冷却介质的分类与选择原则420
二、淬火冷却介质的性能和质量评判421
三、淬火冷却介质的检测方法422
第五节 油冷却介质423
一、一般淬火油424
二、专用淬火油425
三、真空淬火油428
四、淬火油的氧化/老化429
第六节 水及水溶性淬火介质430
一、水及无机物水溶性淬火介质430
二、有机聚合物水溶液淬火介质432
第七节 淬火介质的使用和维护435
一、淬火油常见问题及解决对策435
二、水基淬火液常见问题及解决对策436
第七章 典型零件热处理438
第一节 机床零件热处理438
一、机床导轨热处理438
二、机床主轴热处理439
三、机床丝杆热处理441
第二节 汽车、拖拉机及动力机械零件热处理441
一、汽车、拖拉机零件热处理441
二、动力机械零件热处理446
第三节 大件热处理456
一、大型锻件热处理456
(一)大型锻件的冶金特点456
(二)大型锻件的锻后热处理456
(三)大型锻件的最终热处理458
二、轧辊热处理467
(一)热轧锻钢工作辊热处理467
(二)冷轧锻钢工作辊热处理469
(三)冷硬铸铁轧辊热处理470
三、大型重载齿轮渗碳淬火472
(一)大型重载齿轮的服役条件与失效形式472
(二)大型重载齿轮的热处理质量控制472
(三)大型重载齿轮渗碳淬火工艺472
四、汽轮机零件热处理473
(一)汽轮机零件的常用热处理工艺473
(二)部分汽轮机零件的热处理474
第四节 量、刃具热处理477
一、量具热处理477
(一)游标卡尺尺身和尺框热处理477
(二)标准硬度块热处理478
二、刃具热处理479
(一)锥柄麻花钻热处理479
(二)机用丝锥热处理481
(三)齿轮滚刀热处理483
(四)高速切削滚刀热处理484
(五)剃齿刀热处理486
(六)拉刀热处理486
第五节 模具热处理489
一、模具的工作条件、性能要求及材料489
二、常用模具钢的预备热处理492
三、常用模具钢的热处理工艺495
四、典型模具热处理实例500
(一)塑料模具500
(二)冷作模具501
(三)热作模具503
第六节 紧固件、滚动轴承零件热处理506
一、紧固件热处理506
二、滚动轴承零件热处理509
(一)滚动轴承的结构、服役条件和失效形式509
(二)轴承材料的基本要求509
(三)滚动轴承零件热处理的特点510
(四)相关标准510
(五)滚动轴承钢的常规热处理511
(六)轴承零件的表面热处理515
(七)滚动轴承零件的渗碳淬硬处理515
第八章 热处理件的质量检测及评定分析517
第一节 常用力学性能试验517
一、力学性能试验的取样及制作517
二、金属拉伸试验517
三、金属弯曲试验522
四、金属冲击试验524
五、其他力学性能试验526
六、影响金属材料力学性能的因素533
第二节 硬度试验536
一、金属布氏硬度试验536
二、金属洛氏及表面洛氏硬度试验539
三、金属维氏硬度试验541
四、金属肖氏硬度试验543
五、金属里氏硬度试验544
六、其他硬度试验(努氏、韦氏)545
七、各种硬度值之间的换算及硬度与强度的换算546
八、钢铁热处理件的硬度检验通则546
第三节 无损探伤547
一、磁粉探伤547
二、超声探伤549
三、渗透探伤551
第四节 金相分析与评定552
一、取样与制作552
二、非金属夹杂物含量测定555
三、金属材料晶粒度评定557
四、带状组织(偏析)评定558
五、魏氏组织评定559
六、球粒状珠光体(球化体)评定560
七、马氏体组织评定562
八、残余奥氏体含量评定568
九、碳化物级别评定569
十、化学热处理件铁素体评定571
十一、化学热处理渗层深度金相测定573
十二、渗金属层检验574
十三、过热、过烧组织评定(工具钢、铝合金)574
十四、有效硬化层及硬化层深度的测定575
第五节 金属材料化学分析方法576
一、取样方法与规定576
二、常用化学分析方法577
三、微区成分分析方法579
四、化学分析的允许偏差579
第六节 钢的火花鉴别584
一、火花鉴别的原理584
二、火花鉴别的设备和方法584
三、钢件火花的特征585
四、钢种推定顺序588
五、常用钢火花参考图589
第七节 热处理工艺质量检验591
一、正火与退火工件的质量检验591
二、淬火与回火工件的质量检验592
三、渗碳及碳氮共渗工件的质量检验592
四、渗氮及氮碳共渗工件的质量检验594
五、感应加热淬火件的质量检验596
第八节 热处理件相关失效分析方法598
一、失效和失效类型598
二、失效分析基本思路599
三、失效分析基本程序600
四、热处理件常见缺陷及对失效行为的一般影响600
五、裂纹的基本分析601
六、宏观断口的基本识别604
七、微观断口的基本识别607
八、热处理件的畸变及基本测量609
第九章 热处理通用设备610
第一节 加热设备610
一、电阻炉设备编号610
二、电阻炉的主要类型610
(一)箱式电阻炉610
(二)井式电阻炉612
(三)台车式电阻炉614
(四)井式渗碳炉616
(五)盐浴炉617
(六)流态粒子炉623
(七)离子渗氮设备625
三、燃料炉627
第二节 冷却设备637
一、淬火槽637
(一)淬火冷却水槽637
(二)淬火冷却油槽638
(三)淬火冷却浴槽639
(四)淬火槽的主要附加装置640
二、喷雾冷却和喷液冷却装置641
三、循环冷却系统641
(一)循环冷却系统的类型641
(二)循环冷却系统的组成642
四、冷处理设备647
第三节 辅助设施649
一、工装夹具649
(一)工装夹具的设计原则649
(二)常用的工装夹具649
二、起重运输机械653
三、喷砂机653
第四节 热工仪表653
一、传感器(温度测量元件)与温度计654
二、温度显示与调节仪表663
三、温度控制系统的应用669
四、热处理炉内的气氛控制系统672
五、无纸记录仪675
六、流量计676
七、压力测量仪表677
第五节 筑炉材料678
一、耐火材料678
二、保温材料685
三、耐热构件用金属材料687
四、电热材料与电热元件688
第十章 热处理安全、卫生、环保要求及节能702
第一节 热处理生产的安全、卫生要求702
一、热处理生产中危险因素及有害因素702
二、热处理生产中危险或有害的生产物料和剩余物料703
三、热处理生产厂房及作业环境的安全及卫生要求703
(一)厂房建设要求703
(二)热处理作业环境要求704
四、热处理工作场所空气中有害物质的限值(GB/T27946—2011)704
(一)现行热处理工作场所空气中的有害物质704
(二)热处理工作场所空气中有害物质的容许浓度705
(三)热处理工作场所空气中有害物质的检测706
(四)热处理工作场所空气中有害物质的处理及排放706
五、热处理生产装置的安全、卫生要求706
(一)电阻炉706
(二)燃料炉706
(三)感应加热装置(GB5959.3—2008)706
(四)真空热处理设备707
(五)气体发生装置707
(六)淬火、回火油槽707
(七)盐浴炉708
(八)等离子体热处理设备708
(九)激光热处理设备708
(十)冷处理设备708
(十一)清洗设备708
(十二)喷砂、喷丸设备708
(十三)校正装置708
(十四)夹具、工装及辅助设施708
六、热处理工艺作业的安全、卫生要求708
(一)整体热处理708
(二)表面热处理709
(三)化学热处理709
(四)真空热处理709
(五)盐浴热处理710
七、热处理生产中的消防及防爆710
(一)消防710
(二)防爆712
八、热处理安全、卫生防护技术措施及管理措施712
(一)热处理安全、卫生防护技术措施712
(二)热处理安全、卫生管理措施713
第二节 热处理的环境保护技术要求及环保治理714
一、热处理环境污染的分类和来源714
二、大气污染物的排放与治理715
三、废水控制与治理716
四、固体废物及其无害化处理717
第三节 节能及热处理能耗718
一、热处理的节能途径718
二、热处理的工艺电耗与综合工艺电耗的计算719
三、热处理电炉节能监测721
四、热处理电热设备的节能减排管理722
五、热处理能耗限额723
新技术展望725
展望一 用于超高强度钢的淬火-碳分配-回火(沉淀)(Q-P-T)工艺&徐祖耀725
一、Q-P工艺和Q-P-T工艺725
二、Q-P-T钢的显微组织、性能、成分和热处理设计725
三、Q-P-T工艺的典型应用726
展望二 计算机模拟在热处理中的应用&潘健生 顾剑锋727
一、导言727
二、回顾727
三、热处理计算机模拟的应用实例728
四、计算机模拟在热处理上应用的前景747
展望三 淬火-分配-回火工艺的发展及其在工程中的应用&戎咏华749
一、Q-P-T工艺及其优点750
二、高强塑性Q-P-T钢及其增塑机制751
三、Q-P-T工艺的发展754
四、MQ-P-T工艺用于工件处理的基础和应用实例756
五、MQ-P-T工艺工程应用实例759
附录764
附录一 热处理专业名词解释764
一、总类764
二、退火、正火类766
三、淬火类767
四、回火类769
五、固溶热处理类770
六、渗碳类770
七、渗氮类771
八、渗其他非金属类及渗金属类772
九、共渗类772
十、表面处理及复合热处理类773
十一、沉积及激光类773
十二、组织类774
十三、缺陷及失效类776
十四、热处理设备类777
附录二 标准代号及常用计量单位779
一、标准代号779
二、热处理常用计量单位779
附录三 常用结构钢、工模具钢、不锈耐热钢和铸铁的化学成分及中外牌号对照780
一、常用结构钢的化学成分和中外钢号对照780
二、常用工模具钢的化学成分和中外钢号对照784
三、常用不锈钢、耐热钢的化学成分和中外钢号对照786
四、常用铸铁的化学成分和中外牌号对照787
附录四 国内外部分高速钢、粉末冶金高速钢的牌号、淬火温度与硬度789
一、国内外部分高速钢的牌号、淬火温度与硬度789
二、粉末冶金高速钢的牌号、淬火温度与硬度790
附录五 不锈钢、耐热钢新旧牌号对照791
附录六 铸造形变铝、铜、钛、镁合金中外牌号对照793
一、铸造铝合金的中外牌号对照793
二、变形铝及铝合金的中外牌号对照794
三、铜合金的中外牌号对照795
四、镁合金的中外牌号对照796
五、钛合金的中外牌号对照796
附录七 洛氏、表面洛氏、肖氏与布氏、维氏硬度换算对照797
一、洛氏硬度HRC与其他硬度的换算对照797
二、黑色金属各种硬度之间的换算798
三、肖氏硬度与洛氏、布氏、维氏硬度的换算800
附录八 里氏硬度计检定规程801
附录九 调质、轴类、套类及不同钢材套类零件热处理时需预留的加工余量802
一、调质件的加工余量802
二、轴类零件热处理时外圆预留的磨削余量803
三、套类零件热处理时预留的磨削余量803
四、不同钢材套类零件的预留余量804
附录十 常用钢材水、油、分级、等温淬火及按表面至半马氏体组织深度所确定的临界淬火直径805
一、常用钢材淬火后表面硬度HRC与截面厚度或直径的关系805
二、常用钢材在不同介质中淬火及分级淬火时的临界尺寸806
三、常用钢材等温淬火的最高硬度和最大有效厚度806
四、按表面至半马氏体组织的深度作为淬透性的判断标准的淬火临界直径806
附录十一 钢的热处理工艺经验公式808
一、热处理相变点的计算808
二、钢的临界冷却速度的计算809
三、钢预冷淬火时空气预冷时间ty(s)和Ms点以上分级冷却时间tf(s)的计算809
四、钢的淬火硬度计算809
五、钢回火后的硬度计算810
附录十二 化学元素周期表811
参考文献812