图书介绍
现代高炉操作PDF|Epub|txt|kindle电子书版本网盘下载
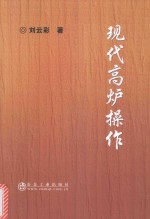
- 刘云彩著 著
- 出版社: 北京:冶金工业出版社
- ISBN:9787502472337
- 出版时间:2016
- 标注页数:358页
- 文件大小:40MB
- 文件页数:374页
- 主题词:高炉炼铁
PDF下载
下载说明
现代高炉操作PDF格式电子书版下载
下载的文件为RAR压缩包。需要使用解压软件进行解压得到PDF格式图书。建议使用BT下载工具Free Download Manager进行下载,简称FDM(免费,没有广告,支持多平台)。本站资源全部打包为BT种子。所以需要使用专业的BT下载软件进行下载。如BitComet qBittorrent uTorrent等BT下载工具。迅雷目前由于本站不是热门资源。不推荐使用!后期资源热门了。安装了迅雷也可以迅雷进行下载!
(文件页数 要大于 标注页数,上中下等多册电子书除外)
注意:本站所有压缩包均有解压码: 点击下载压缩包解压工具
图书目录
绪论——炼铁的过去和现在1
0.1 炼铁的起源和发展1
0.1.1 块炼铁——古老的炼铁方法2
0.1.2 高炉的发明——炼铁生产的第一次革命5
0.1.3 高炉起源于炼铜炉5
0.2 高炉冶炼的发展6
0.2.1 战国到西汉,高炉容积扩大期6
0.2.2 强大的生产组织和质量管理7
0.2.3 鼓风设备和椭圆高炉的发明9
0.2.4 熔剂的使用11
0.2.5 我国公元以前年代铁的化学成分12
0.2.6 东汉到明朝——新技术创造期14
0.3 我国古代炼铁和欧洲炼铁比较18
0.3.1 我国高炉炼铁的重要创造19
0.3.2 欧洲高炉发展19
0.3.3 欧洲炼铁水平后来居上21
0.3.4 高炉生产水平的变迁22
0.3.5 高炉最早出现在中国的原因24
0.4 直接还原——块炼铁的“复活”24
0.4.1 直接还原铁生产的主要国家24
0.4.2 直接还原铁生产的主要方法25
0.4.3 转底炉法27
0.5 熔融还原——炼铁二次革命28
0.5.1 Corex法28
0.5.2 Finex法29
0.5.3 HIsmelt法30
0.6 结语31
参考文献31
1 高炉生产概论35
1.1 炼铁在钢铁企业中的地位35
1.2 决定高炉生产水平的条件35
1.3 高炉操作的任务37
1.3.1 高炉顺行、稳定37
1.3.2 合理使用炉料38
1.4 高炉顺行、稳定的前提38
参考文献41
2 活跃炉缸42
2.1 焦炭燃烧区与鼓风动能43
2.1.1 焦炭燃烧区43
2.1.2 鼓风动能与回旋区45
2.1.3 鼓风动能与风速47
2.2 下部调剂47
2.2.1 风量水平48
2.2.2 风速或鼓风动能的确定49
2.2.3 风速、鼓风动能和冶炼强度的关系50
2.2.4 回旋区长(深)度51
2.2.5 回旋区的作用54
2.2.6 风口长度55
2.2.7 风口角度56
2.2.8 堵风口操作57
2.2.9 理论燃烧温度57
2.3 合适风速(鼓风动能)的经验判断与调剂58
2.4 风口烧损和预防58
2.4.1 风口烧熔的原因60
2.4.2 风口破损的处理61
2.5 炉缸堆积和预防62
2.5.1 炉缸堆积的征兆62
2.5.2 炉缸堆积的主要原因64
2.5.3 炉缸堆积的处理原则和方法70
2.5.4 预防炉况失常的措施76
参考文献77
3 料柱结构与控制煤气分布79
3.1 高炉料柱结构80
3.1.1 炉料特征80
3.1.2 高炉布料的作用81
3.2 炉料分布和煤气分布82
3.2.1 炉料分布和软熔带82
3.2.2 软熔带高度84
3.3 观察与判断煤气流分布86
3.3.1 径向煤气流速和煤气温度86
3.3.2 直接观察88
3.3.3 仪表综合判断89
3.3.4 由非正常炉况判断煤气分布91
3.4 适应高炉冶炼条件的煤气分布91
3.4.1 选择适应冶炼条件的煤气分布91
3.4.2 确定相应的炉料分布92
3.4.3 料线和批重92
3.4.4 利用装料制度改善顺行94
3.4.5 提高煤气利用率——由Ⅱ型煤气分布变Ⅲ型95
3.5 炉料分布计算99
3.5.1 布料落点计算公式99
3.5.2 布料落点计算程序使用说明100
3.6 边缘气流与中心气流调控104
3.6.1 边缘煤气分布的危害104
3.6.2 中心煤气流控制105
3.6.3 取消中心加焦107
3.7 渣皮脱落108
3.7.1 渣皮脱落的特征108
3.7.2 渣皮脱落与边缘管道111
3.7.3 铜冷却壁与渣皮脱落112
3.7.4 渣皮脱落的危害112
3.8 上下部调剂相适应113
参考文献115
4 稳定炉温117
4.1 铁水特性117
4.1.1 铁水的熔点117
4.1.2 温度对碳溶解度的影响118
4.1.3 不同元素对碳溶解度的影响118
4.1.4 现代高炉铁中含碳量119
4.1.5 铁水中的微量元素120
4.2 铁水在炉缸的状态121
4.2.1 实测炉缸铁水状态121
4.2.2 铁水成分波动121
4.2.3 铁水成分波动幅度的确定123
4.3 控制炉温123
4.3.1 判断炉温的指标123
4.3.2 炉温判断124
4.3.3 影响炉温的主要参数125
4.3.4 各参数的作用时间127
4.3.5 炉温控制的方法128
4.3.6 料速变化129
4.4 喷煤操作129
4.4.1 我国的喷煤129
4.4.2 煤粉的作用132
4.4.3 煤粉燃烧133
4.4.4 喷煤对冶炼周期的影响134
4.4.5 用煤粉调剂炉温134
4.5 低硅铁冶炼136
4.5.1 低硅铁生产136
4.5.2 我国的实践139
4.6 炉缸冻结及处理139
4.6.1 炉缸冻结的原因及类型140
4.6.2 称量错误导致的炉缸冻结141
4.6.3 炉缸冻结的处理方法145
4.6.4 净焦量146
4.7 改铁操作146
4.7.1 炼钢铁改铸造铁146
4.7.2 铸造铁改炼钢铁148
4.7.3 改铁总结149
4.8 调剂炉温的专家系统149
4.8.1 高炉过程自动控制的开发研究149
4.8.2 高炉专家系统152
参考文献153
5 控制炉渣成分155
5.1 铁水质量控制156
5.1.1 铁中硫的危害156
5.1.2 硫的分布及计算公式156
5.1.3 炉渣碱度160
5.1.4 硫分配系数的比较161
5.2 稳定的炉渣和黏度164
5.2.1 稳定的炉渣164
5.2.2 MgO对炉渣黏度的影响165
5.2.3 McCaffery黏度图分析166
5.2.4 炉渣中Al2O3和MgO比例的确定168
5.3 特殊功能炉渣169
5.3.1 清理结瘤170
5.3.2 利用炉渣排出碱金属171
5.3.3 利用炉渣处理贫矿174
参考文献177
6 出铁出渣179
6.1 高炉上推力180
6.1.1 上推力的作用180
6.1.2 保持高炉上推力稳定180
6.2 出铁181
6.2.1 铁水在炉缸的运动181
6.2.2 出铁速度182
6.2.3 铁水黏度183
6.2.4 连续出铁184
6.3 出渣185
6.3.1 炉渣在炉芯带内的流动185
6.3.2 不放上渣185
6.3.3 稳定上推力186
6.4 出铁过程排出的气体188
6.5 深刻的教训189
参考文献190
7 高炉基本操作191
7.1 炉料下降运动192
7.2 直接观察和操作曲线识别194
7.2.1 高炉工长的贡献和作用195
7.2.2 合理追求,务实操作195
7.2.3 把握时机,当机立断198
7.3 管道199
7.3.1 形成管道的原因199
7.3.2 管道的处理200
7.3.3 罕见的真实管道200
7.3.4 管道的类别和特征200
7.3.5 管道与偏尺203
7.4 塌料与悬料205
7.4.1 管道与塌料205
7.4.2 悬料机理207
7.4.3 料尺分类209
7.4.4 悬料的处理与教训210
7.4.5 难行状态下的加风217
7.4.6 难行亏尺或坐料后亏尺的加料218
7.5 操作教训219
7.5.1 控制放风219
7.5.2 坐料后的放风219
7.5.3 低炉温时的坐料219
7.6 高炉顺行指数220
7.6.1 顺行的炉况220
7.6.2 利用顺行指数比较本厂高炉的顺行水平222
7.7 异常炉况的专家系统223
参考文献224
8 高炉烧穿的预防和处理226
8.1 炉缸烧穿是一个过程226
8.1.1 炉缸在哪里经常烧穿?226
8.1.2 “突然”烧穿的原因229
8.1.3 减少象脚型侵蚀229
8.1.4 出铁速度232
8.1.5 重点检测哪里?232
8.2 炉缸烧穿及处理233
8.2.1 炉缸烧穿前的征兆233
8.2.2 侵蚀速度234
8.2.3 减小烧穿损失237
8.2.4 烧穿后的修复238
8.3 炉底烧穿240
8.3.1 事故经过240
8.3.2 合理的炉底结构242
8.3.3 铅渗透和炉底冷却装置的破坏243
8.3.4 炉底冷却装置的检查245
8.4 陶瓷杯结构245
8.4.1 陶瓷杯的实践246
8.4.2 我国专家对陶瓷杯结构的争议249
8.4.3 陶瓷杯炉底炉缸结构的优势251
8.5 补炉操作252
8.5.1 对预防烧穿操作方法的评价252
8.5.2 用含钛炉料补炉的历史253
8.5.3 钛回收率255
8.5.4 钛化物在炉缸的形成与沉积256
8.5.5 为什么补炉后依然烧穿?260
8.5.6 含钛炉料补炉效果264
8.5.7 补炉操作的优点和缺点264
8.6 炉体膨胀和炉皮开裂265
8.6.1 炉皮开裂265
8.6.2 开裂原因266
8.6.3 避免开裂的措施267
8.6.4 膨胀导致的炉皮开裂267
8.7 灌浆、压入和喷涂造衬267
8.7.1 灌浆268
8.7.2 热面灌浆268
8.7.3 硬质料压入造衬269
8.7.4 喷涂造衬269
8.8 预防炉体破损271
8.8.1 高炉结构决定高炉寿命271
8.8.2 炉衬材质271
8.8.3 冷却系统272
8.8.4 施工质量272
8.8.5 控制有害元素入炉量273
8.8.6 补炉操作273
8.8.7 争取时间的临时措施273
8.8.8 合理烘炉274
8.8.9 完善、严格检测制度274
参考文献274
9 高炉结瘤277
9.1 结瘤的征兆278
9.1.1 结瘤部位的隔热278
9.1.2 结瘤改变炉料分布280
9.1.3 结瘤对炉缸的影响283
9.1.4 结瘤后的操作特点283
9.1.5 结瘤特征284
9.2 炉瘤的组织结构和形成过程285
9.2.1 炉瘤的组织结构285
9.2.2 炉瘤的物理特性286
9.2.3 炉瘤中粘结相的作用286
9.2.4 炉瘤的形成287
9.3 炉瘤位置的判断288
9.3.1 探孔法288
9.3.2 传热计算法289
9.3.3 降料面观察法289
9.4 结瘤的处理289
9.4.1 高炉炉瘤是运动的,能增长,也能脱落290
9.4.2 洗炉291
9.4.3 降料面法处理炉墙结瘤295
9.4.4 爆破除瘤297
9.5 预防结瘤301
参考文献305
10 开炉操作307
10.1 开炉前的准备工作307
10.1.1 人员配备与培训307
10.1.2 设备试车与验收307
10.1.3 炉料和备品、备件准备307
10.1.4 上下工序的状况调研308
10.2 烘炉308
10.2.1 热风炉烘炉308
10.2.2 高炉本体烘炉准备309
10.2.3 烘炉温度控制311
10.2.4 烘炉结束与凉炉312
10.2.5 严格操作,杜绝事故313
10.3 开炉的冶炼指标和配料计算313
10.3.1 开炉总焦比和开炉料的选择313
10.3.2 计算方法314
10.4 全焦开炉315
10.5 含铁炉料的位置317
10.6 装炉及测料面318
10.6.1 装料前的工作318
10.6.2 按计划安排次序加料318
10.6.3 合理布料,应从开炉填料时开始318
10.6.4 测量料面320
10.7 点火与送风320
10.7.1 点火烘料操作320
10.7.2 风口参数选择321
10.7.3 点火323
10.7.4 加料326
10.7.5 送气328
10.8 出铁328
10.8.1 出铁时间的确定328
10.8.2 出第一次铁应考虑开铁口所需时间330
10.8.3 有些厂在开炉出铁方面的创造330
10.9 后续操作330
10.9.1 改变装料330
10.9.2 加负荷条件与加负荷330
10.9.3 降铁水含硅量速度330
10.9.4 加风速度331
10.9.5 加风过程与装料制度相适应331
参考文献331
11 停风、封炉和停炉332
11.1 短期停风333
11.1.1 短期停风特点333
11.1.2 短期停风操作程序333
11.1.3 短期停风后送风程序333
11.1.4 停送风注意事项334
11.2 突然停风334
11.2.1 突发事故的停风335
11.2.2 紧急停水335
11.2.3 鼓风机突然停风336
11.2.4 紧急停电336
11.3 长期停风336
11.3.1 停风准备工作337
11.3.2 停风程序(第一步)337
11.3.3 炉顶点火337
11.3.4 停风程序(第二步)338
11.3.5 长期停风注意事项339
11.4 降料面339
11.4.1 停气降料面的缺点339
11.4.2 全风降料面实践340
11.5 封炉341
11.5.1 封炉要点341
11.5.2 封炉实例342
11.5.3 经验教训344
11.5.4 封炉小结345
11.6 停炉345
11.6.1 安全、快速降料面345
11.6.2 利用煤气成分变化判定料面深度345
11.6.3 控制煤气中H2、O2量,杜绝煤气爆震346
11.6.4 放出全部残铁348
参考文献351
12 高炉爆炸352
12.1 煤气爆炸353
12.1.1 高炉煤气爆炸的必要条件353
12.1.2 1号高炉炉内煤气爆炸的原因353
12.1.3 混合形成爆炸煤气后发生的爆炸354
12.1.4 预防煤气爆炸355
12.1.5 炉内打水爆震和爆炸356
12.2 铁水遇水发生爆炸357
参考文献358